Is the future of AM hybrid?
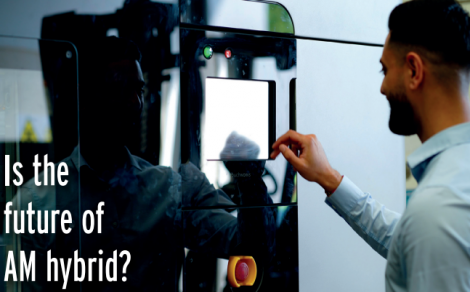
Joe Godfrey, 3D print specialist at Tri-Tech 3D, explores how balancing in-house and outsourced additive manufacturing (AM) can enhance onshoring efforts.
According to a UK Parliamentary report, the manufacturing sector accounted for 9.8% of total UK economic output and 8.1% of jobs between July and September 2022. Following Brexit and a global pandemic, more manufacturers are onshoring to reduce reliance on imports while reevaluating production processes.
Today, over 50% of engineers use 3D printing to produce end-use functional parts and this interest in AM has been sparked not least by the rising cost of traditional manufacturing processes. The costs of raw materials are continuing to rise — for example, British Steel began 2023 with a £75 per tonne price hike. The cost of energy is on the up, making it more expensive to power CNC machines and other equipment, while labour shortages remain an issue.
The growing availability of sophisticated AM systems, combined with the lack of waste they produce and the improved part reliability they provide, has improved the ROI of AM. Meanwhile, the 3D printing capabilities that manufacturers can bring in-house continues to grow. For example, stereolithography (SLA) AM systems create parts layer by layer using a UV laser and a vat of liquid UV-curable photopolymer resin, enabling users to expand their design capabilities and improve part finish and quality in shorter build times.
The importance of outsourcing
When investing in any AM system, the business justification is key. Building a capital expenditure justification is challenging when manufacturers are unclear on what the final costs are likely to be. Therefore, outsourcing to a bureau before purchasing a printer for the shop floor can make the most financial sense and make it easier to demonstrate value.
Traditionally, most AM systems were small and limited in build size. Therefore, a purely in-house arrangement was unlikely to satisfy all production needs, especially if the business only purchased the one machine. Say the manufacturer was also working on a specific application that required a good surface finish. The manufacturer may already own a thermoplastic FDM printer, but that wouldn’t deliver the required finish — instead, they would need to outsource that part to a bureau that could print it quickly and to injection moulding quality. Rather than injection moulding the part as a one off, the manufacturer can still benefit from the advantages that AM offers — flexible design, minimal waste and part strength — without worrying about the limits of in-house capability.
Why the future is hybrid
According to a 2022 survey by Make UK, 22.8% of firms said that bringing production capacity to the UK was a priority for them — so what will this look like when using AM? Working with a 3D printing bureau can make the most financial sense, but this shouldn’t come at the expense of in-house innovation. By printing the bulk of their products in-house, manufacturers can produce complex geometries flexibly and cost effectively while rapidly prototyping new designs in parallel. Meanwhile, they can protect profit margins and safeguard intellectual property (IP). At our 3D print bureau, we actually talk to our customers about how they can bring some processes in-house.
In-house and outsourced 3D printing don’t have to compete, they can dovetail. Printing using their own AM systems on the shop floor gives manufacturers added control and oversight, but UK-based bureaus can provide vital support by quickly producing any overspill parts. Therefore, even if internal capacity is limited, manufacturers can still receive components — sometimes in as little as 48 hours.
Following supply chain issues over the last few years, onshoring is an attractive strategy. AM can help onshoring efforts by reducing lead times, minimising waste and improving productivity, thus competitiveness. By developing an in-house production strategy while outsourcing certain parts to bureaus, manufacturers can get the best of both worlds — production flexibility, short lead times and enhanced part quality
https://www.linkedin.com/company/tri-tech3d/
-
Smart Manufacturing & Engineering Week
05 - 06 June, 2024
NEC, Birmingham -
HILLHEAD 2024
25 June, 2024, 9:00 - 27 June, 2024, 16:00
Hillhead Quarry, Buxton, Derbyshire UK