Safeguarding your compressed air assets
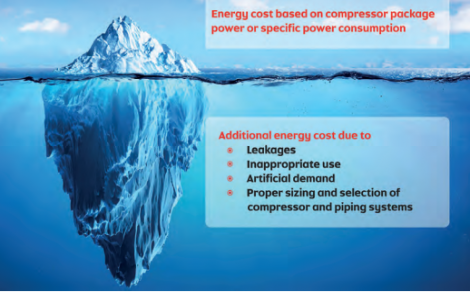
By David De Pril, director, product management and marketing, ELGi
Energy efficiency is increasingly important for us all as it directly relates to costs. Increasing regulatory pressure is also on the horizon in the form of the EU Commission’s proposed revision to the EU Energy Efficiency Directive (EED). The revised EED will make the EU’s energysaving objective legally binding, obliging EU countries to collectively reduce their energy consumption by 9% below 2020 levels by 2030. Additionally, EU countries will likely have to achieve new annual savings of 1.5% of total energy consumption as of 2024, up from the current level of 0.8%.
In manufacturing processes using compressed air, energy efficiency improvements are critical since air compressors consume approximately 12% of electrical energy. What’s more, over the lifespan of an air compressor, 80% of the cost is energy use, and 20% is the cost of the unit. However, do compressed air users have the big picture of where these costs come from and what contributes to them?
Looking beyond the system
There are many technical and economical choices when taking the right approach to reducing the energy intensity of compressed air systems. Not so long ago, the industry focus rightly looked beyond the unit efficiency to the system and system efficiency. Greater awareness of operational needs and the increased pressure to reduce energy use and improve efficiency prompt a closer examination of the system. More granularly, how do we balance operational needs, capital costs, the lifespan of critical assets, and energy use?
The traditional total cost of ownership (TCO) approach looks at the energy cost based on a compressor package’s power or specific power consumption. Whereas a complete operational analysis looks at everything from the compressor to the environment in which it operates, as well as operational demands such as peaks and troughs in air demand and operational expansion planning. A finite analysis of the bigger picture – understanding how even the most minor system elements impact the energy consumption associated with the compressor.
The aim is to strike the right balance in technical and economic choices - in compressor units, capacities, operational parameters, energy efficiency, planning for future air demand changes, and considering energy costs related to leakages, inappropriate use of air, artificial demand, etc.
Compressed air users need to look at their operational demand and see what compressed air is necessary for their specific operation throughout the production cycle. Then they should study how to optimise the compressor room and question the hardware and the settings of the compressed air installation. After this study, compressed air users can truly safeguard their assets, investments, and energy costs and ultimately achieve a new low in compressed air TCO.
Close, but let’s take a wider look at safeguarding your assets
To describe it better, let’s take a look at a hypothetical process when a customer considers expanding its manufacturing site, adding another production line, increasing its manufacturing capacity, etc. In such a case, a typical discussion between the compressed air user and air compressor supplier about the new compressed air demands starts with the customer’s request for more air assuming that an additional or larger compressor is the solution. The thing is, simply adding another compressor is not the answer when the surrounding system stays the same. This can result in too much stress executed on the system’s existing structure and can lead to reduced overall efficiency. Why?
When a manufacturing plant or line is being built, a compressed air system is planned and designed to fit the capacity load of a particular production process. It all works as planned and achieves planned results. When the company’s operations grow, and the plant increases production, the air-demands change. And adding another compressor to fit the increasing needs is not the answer. Before even considering that compressed air users should work with the experts to conduct a detailed analysis of how the current system is performing at a given time and within given demands. Before any decision is made, a holistic analysis of the entire production system, historical and planned air requirements, current piping, and checks for leaks should be done.
Quite often, the expansion of a manufacturing site or production line won’t even require adding another compressor. Finetuning the existing assets to run at proper and adapted loads – not at the highest pressures or extreme duties – can result in lowered pressure on the entire system and reduce energy consumption. It’s an easy route to add another compressor, but taking a holistic approach, analysing and optimising the existing system and its elements, is the key to safeguarding your assets and achieving the desired energy efficiency improvements.
Let’s Audit, Right-Size, and Implement
Before making a decision on what to do, whether to replace a compressor, add another one, or adjust the existing system, an audit of the operations is necessary. A compressed air auditor can check the entire system and establish the input, the state of the compressor units and how they are running, and what exact pressures are required. This will paint a picture of the system with its surroundings, elements, pipework, and critical consumption. With this knowledge, we can move to the next step, which is making an educated decision on how to optimise it to meet the new requirements. Very often, the new, expanded production requirements can be met with the same power but adjustments to the airflow (of course, depending on the size of the expansion). It’s all about rightsizing the air needs.
Let’s show this based on a concrete example. A plant with current compressed air demand is expanding its operations and requires an increase of up to 35% in compressed air. Our job is to see how this additional compressed air demand can be achieved and whether adding a new compressor is necessary. The audit shows the system’s current state, including piping, running pressures throughout the day, and the cyclical changes in demands. The next step is to see how the existing system can be optimised to generate the additional demand within the same power. This can be done by analysing and rightsizing the system and taking a closer look at:
Impact of leakage – Leakage happens throughout the system over time. It can be caused by aging hoses, improper joints, installations, wrong parts, or corrosion. We estimate that even 20 to 30% of compressed airflow can be lost due to leakage. Leakage via a 3 mm (~1/8”) hole can consume 4 kW/h of electricity, incurring an annual loss of 19,200 kW (at 7 bar g. (100 psi g.) 16 hrs/day for 300 days in a year). This is creating enormous room for improvement. Leaks occurring in pipe joints and connections can be prevented by simple, appropriate tightening and proper seals and sealing media. Suitable quality fittings, tubing, and connections last longer. An audit can establish risk areas while having a leak detection and maintenance programme at regular intervals will reduce future leakages.
Inappropriate use of compressed air can mean many simple and ordinary things like blowing off washed parts or even operators who work in a dusty environment and use the compressed air supply to blow off the dust from their clothing. These things happen.
Checking and eliminating inappropriate use of compressed air throughout the plant can contribute significant gains.
Artificial demand is the excess volume of air required by unregulated end-uses as a result of supplying higher pressure than necessary for applications. This equals an unnecessary consumption of energy. A simple strategy of performing the proper selection, installation, and use of pressure controllers on top of preventing leaks and inappropriate use can be of great help here.
Optimizing the pressure band - Setting the correct pressures can be done by establishing and understanding the requirements, determining pressure losses in the piping system between the compressor and the production equipment, setting the proper load and unload pressure as low as possible to meet application demands. The savings of reducing 1 bar (14.7 psi) of compressor set pressure is even 7% of the total compressor power consumption. Annually, with 16hrs/day of operation for 300 days a year, a 7%
savings in case of 110KW compressor power consumption equals 36,960 kWh.
Minimising pressure loss - While no system can be without a pressure loss occurring in the piping system and downstream equipment – the pressure difference between the point of discharge from the compressor and point of consumption – can be
minimised and kept as low as possible. It starts with the piping design – placing the production and application points close to each other and optimising the size and shape of the piping. Downstream equipment should be selected at the lowest pressure drop,
and maintained following the air compressor supplier recommendations, and cleaned periodically. All this keeping in mind that loss of 1 bar of pressure will incur 7% of the total energy consumption of a compressor.
A properly executed audit with the right partner will show a complete consumption pattern of compressed air over time, helping with leakage detection, compressor sizing, and energy optimisation, ultimately using the data to make the right decision about the ongoing operations future expansion of the system.
Whether compressed air users, air compressor suppliers, service teams, or operators – we can all improve the energy efficiency, system efficiency, and costs by looking beyond system efficiency to optimise compressed air demand and supply. The added benefit of this approach pays off by safeguarding your assets, reducing the risk of downtime and maintaining efficient operations.
https://www.linkedin.com/company/elgi-compressors-europe/
-
The Aftermarket Event
02 October, 2024, 9:30 - 03 October, 2024, 15:30
Farnborough International West Entrance, Gate F -
NFPC Annual Industry Exhibition
23 October, 2024, 9:30 - 16:00
Turner Road, Worksop, Nottinghamshire, S81 7AE -
AEMT Awards
21 November, 2024
Double Tree by Hilton Hotel, Coventry -
SMART Manufacturing & Engineering Week
04 - 05 June, 2025
NEC, Birmingham UK