- Home » Editorial » Hydraulics
Hard-to-handle fruit, veg & poultry waste proves easy pickings for Seepex BTM pumps
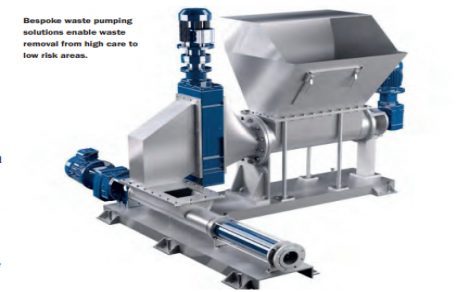
Cost-saving solution
Finally, the BTM pump range is more efficient, generating significant cost savings. By chopping, pumping and transferring all-in-one as the BTM is able to create a pumpable consistency without requiring any additional water, resulting in savings from water usage. This has the additional benefit of reducing the volume of waste by up to 60%, making it easier to transport and thereby cutting transport costs. The operating and energy costs of the BTM are considerably lower than vacuum or compressed air systems, generating savings there. And by removing a manual element from the process and automating it, food producers are saving on labour costs, too, freeing employees for more lucrative, primary production roles.
Where high care production areas are chilled, removing waste via a simple pipeline rather than manually through doorways, will also assist in reducing energy costs as well as minimising potential contamination from external sources.
Bespoke options for most challenging waste streams
Where more challenging by-products need to be transported, customised solutions are available. ‘Bridging’ can be an issue with certain wastes, so the BTM pump range includes augers with a large pitch that enables the product to be conveyed into the cutting elements to ensure continuous pumping. Horizontal and vertical grinders can also be integrated, as can stone and knife traps to prevent pump damage, while dewatering devices can help to reduce waste volume even further. Finally, all BTM pump systems can be fitted with Smart Conveying Technology (SCT); an innovation from Seepex that enables rapid dismantling and cleaning, increasing pump stator life by up to 200% and reducing maintenance time by up to 85%. Pumps fitted with SCT are also suitable for Clean-Out-of-Place (COP) or CIP.
https://www.linkedin.com/company/seepex-uk-ltd/
Case studies
Potato processor
A major vegetable processing company supplying several large retailers approached Seepex for a solution to improve the efficiency of potato waste handling at its UK plant. The waste peelings and reject potatoes were being manually collected and transported by conveyor to a waste holding area. The company needed a safer, more efficient and more hygienic way to transfer the waste, so commissioned Seepex to install a BTM open hopper PC pump, sized to match the maximum daily waste volume.
Within the pump hopper is an auger feed screw, which conveys both viscous and non-flowable waste through the built-in cutters and into the pumping elements of the rotor and stator. The cutting elements comprise rotating and stationary knives on the auger and pump casing, which chop the potato waste to enable to be pumped to the final disposal area. An extended hopper enables the waste to be directly fed from a tote bin-tipper. This reduces handling and the amount of waste spillage onto the floor, improving health and safety. As the site project engineer comments: “Now we hardly have to handle the waste at all – and we’ve got a closed pipeline system instead of our open conveyors.”
-
EIMA International 24
06 November, 2024, 9:00 - 10 November, 2024, 18:30
Bologna, Italy -
AEMT Awards
21 November, 2024
Double Tree by Hilton Hotel, Coventry -
The BCAS luncheon
21 November, 2024
The Grand Hotel, 1 Church St, Birmingham B3 2FE -
LAMMA Show 2025
15 January, 2025, 8:30 - 16 January, 2025, 16:30
NEC, Birmingham UK