- Home » Editorial » Hydraulics
Hydraulic hoses – The advantages of an integrated systems approach
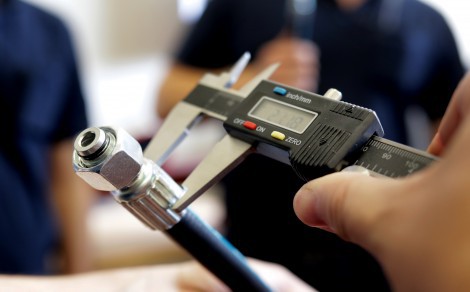
By Cindy Cookson, vice president of hydraulics global product line management, Gates,
If hydraulic equipment fails, manufacturing, construction or warehouse activity can come to grinding halt resulting in inactive machinery and operators, not to mention missed customer deadlines. This is why we believe it is imperative that your hydraulic equipment is sourced from a supplier with an established and proven integrated systems approach to design, manufacture and assembly of hydraulic hoses.
In so doing, you will ensure that the integrity of your hydraulic system is given top priority from the design stage, through to commissioning and installation. Moreover, it is also important that the hydraulic equipment supplier can provide the right level of training in cooperation with all authorised sales partners in order to keep operators abreast of the latest technology and occupational health and safety requirements in the manufacture of hydraulic hose lines. And all this should be complemented by full maintenance guidance and assistance as and when required.
Factory-quality assemblies
At Gates, we are committed to providing a full 360-degree service offering to customers. This starts with our Integrated Systems Approach (GISA) to hose assembly. All elements of this process are designed together to produce factory quality assemblies that perform above and beyond any international standard. This approach is how Gates ensures full compliance with the European Machinery Directive.
Gates MegaSys hoses and couplings not only have many advanced-design features, but they are also manufactured to stringent tolerances, allowing consistently high performance. Moreover, our hoses and couplings are designed, tested and validated together – each with the other in mind, resulting in the hose and coupling interface being a perfect fit.
Wherever the hose is assembled, whether this is at a Gates factory or in the back of a service van, the final product is exactly the same and in accordance with Gates’ high standards – the same hose, the same couplings, the same die sets and the same crimp diameter. Indeed, our partners are producing the very same assemblies that we are providing directly to major OEMs, whether they provide mobile service replacement hose assembly or a complete factory hydraulic installation.
The custom-design advantage
Gates self-assembly machines and dies are custom-designed to work with the MegaSys next-generation range of hose and couplings. Gates dies are characterised by a proprietary profile design for an optimal cylindrical crimp. Gates proprietary die designs also require fewer die sets to crimp our whole range of hoses and couplings, which minimise changeovers and storage space. They are tried, tested and validated to provide you with optimal crimp settings. The die sets are also logically organised to facilitate the most convenient die selection every time.
Beyond international standards
When Gates MegaSys hose and couplings are crimped in accordance with the Gates Integrated System, they yield factory-quality assemblies that are fully compliant to European Directives and legislation exceeding all international standards.
Gates MegaSys wire-braid hoses and MegaCrimp coupling assemblies are developed to withstand impulse testing to 600,000 cycles. Our spiral wire hose and Global Spiral GS coupling assemblies even perform beyond one million cycles.
Recent standards like ISO 18752 about isobaric hoses range are focused on hose performance rather than the reinforcement design, opening up options for hose manufacturers to innovate on their product portfolio. Gates has patented designs with high-density, one wire reinforcement that performs as well as standard two-wire braids, and high-performance two-wire-braid reinforcement that outperforms conventional four-al hoses… with flexibility, compactness and weight advantages. Our recent MXT and MXG 4K hoses range are made according to this application of our material science knowledge, process innovations, and design expertise.
Lower maintenance costs and lower cost of ownership
Gates’ self-assembly machinery programme has been compiled to lower your maintenance costs through grease-free operation. Our MCX crimpers come with a self-lubricating slide bearing system, which eliminates metal-to-metal abrasion between master dies and the crimper head and decreases friction by 20%. An additional result of the self-lubricating slide bearing system is that the working environment becomes cleaner, while dirt and debris are less likely to cause costly downtime, bringing your total cost of ownership of Gates crimpers to even lower levels.
Access crimp settings in seconds
In line with our Integrated System Approach, each Gates crimping machine comes with validated crimp settings for the complete hose and coupling range. This allows users to produce high-quality Gates assemblies themselves, meeting and/or exceeding reference international standards. The European Gates eCrimp database provides the most up-to-date crimp data in just a few clicks. Users can gain fast and easy access to crimping instructions and crimp diameters. There is no need for time-consuming trial-and-error testing or sifting through a stockpile of outdated CD-ROMs to find the ideal machine settings. Simply go to ecrimp.gates.eu or download the mobile eCrimp app (available for Android and iOS) and get immediate access to the crimp library without registration.
Fast, comfortable handling
We believe products that are easy and pleasant to use can improve user productivity. That is why every Gates piece of equipment for crimping, cutting and marking are designed for fast, comfortable handling. In all electrical-driven crimpers, a standard built-in storage rack is positioned for quicker die selection, while die sets are logically organised and within easy reach of the operator. Field service crimping devices are easily portable and come with a detachable die storage case, solid and durable handles and resistant rubber protection layers. Feedback from our user community has shown that ergonomic design is widely appreciated, not in the least because of higher productivity figures and fast approval by local health and safety executives.
Workshop machinery options
In the Gates workshop, safe, fast and efficient assembly of hydraulic hoses and couplings is made simple. All machines are custom designed to work with a well-defined range of Gates hoses and couplings, allowing production of factory-quality assemblies fully complying with European Directives and the most stringent international standards. No matter what your workshop needs, whether you are a starter, a professional or a full-service workshop, Gates has the right product offering for you.
Special proposition for mobile service operations
A Gates hose assembly is much more than the sum of its components, it is the combined result of a rigorous test regime and of a tightly controlled manufacturing process, both at Gates and at the point of assembly. To reduce the risk of premature failure due to variations in the assembly process, Gates has developed a special proposition for mobile service operations allowing them to benefit from the simplified and superior Global range of no-skive hoses and couplings. And thanks to the Gates Integrated System, mobile service operators can offer their customers the superior quality and performance that they deserve.
Factory-quality, no-skive assemblies – even in the field
In the field, every minute counts. In today’s environment, equipment, whether it be agricultural, construction or mining, simply cannot afford unnecessary downtime. This is why Gates has developed a range of small, portable and easy to use crimpers specifically designed for end-users on site. And since these simple, lightweight machines are designed as part of the Gates Integrated System Approach, end-users are assured of factory-quality, no-skive assemblies – even in the field.
Keep efficient, safe and compliant with the right training
Mixing and matching couplings and hoses from different manufacturers can lead to premature assembly failure, as hoses, couplings, assembly equipment and crimping tolerances from different vendors are never guaranteed to offer safe interchangeability. Improper assembly and installation can seriously compromise performance and human safety. If a hydraulic hose assembly fails, the assembler can be held accountable for damages, as stated by European legislation (2006/42/CE - ISO 4413:2010). To help you avoid material and personal hazards and liability issues, Gates Fluid Power Europe can provide you with expert information on safety issues affecting hydraulic hose assemblies through the Safe Hydraulics training programme.
So, with Gates’ Integrated Systems Approach coupled with our dedication to high-quality materials, advanced product features and first-class customer service, we are confident we can help to optimise your operations and bring downtime and maintenance costs substantially while keeping you efficient, safe and legally compliant.
https://www.linkedin.com/company/gates-corporation/
https://twitter.com/gatesindustrial
-
PPMA 2025
23 September, 2025, 9:30 - 25 September, 2025, 16:00
NEC, Birmingham UK -
Advanced Engineering Show 2025
29 October, 2025, 9:00 - 30 October, 2025, 16:00
NEC, Birmingham UK