- Home » Editorial » Hydraulics
Fluid power faux pas
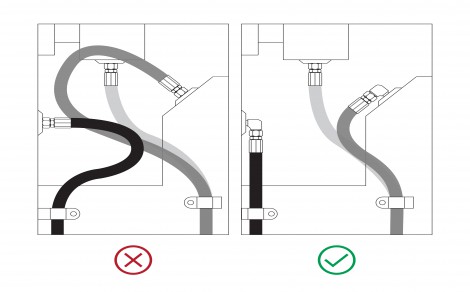
By Cindy Cookson, vice president of hydraulics global product line management, Gates, shares her top five hydraulics system bloopers and some thoughts on what you can do to avoid the same mistakes in your applications.
Over the years, hydraulic hose and coupling system pressures have increased, and the loads on hydraulic systems are increasingly dynamic. Meanwhile, materials science and process technologies have improved the capabilities of hydraulic hose and coupling assemblies. Relying on “what you’ve always used” means you’re missing out on innovation and improvements in hydraulic hoses and couplings, but it could also mean that you’re compromising the safety of your hydraulic system.
Hose and coupling selections should be made based on system requirements and not just on a hose construction. We often hear, “I need a two-wire braid hose” or “my system needs a four-spiral hose”, but as OEMs have transitioned to isobaric hose ratings and hose manufacturers have innovated to deliver flexibility and weight savings in hydraulic hoses, referring to a hose by its construction is a risky move. Instead, Gates advises users to always follow system requirements for working pressure, temperature, and fluid compatibility when selecting hoses and couplings.
To make things easier, the STAMPED acronym is often used as a reminder of the aspects to consider when selecting a hose for a specific application. Here’s a brief explanation of the STAMPED acronym, extracted from Gates Safe Hydraulics course:
• Size – determine what ID hose is required for fluid flow. A hose that is too large will reduce system performance due to increased pressure loss and excessive system heat from excessive fluid turbulence
• Temperature – the hose must be capable of withstanding the system’s minimum and maximum fluid and ambient temperatures.
• Application – how and where the hose assembly will be used.
• Material/Media – the hose tube, cover and couplings must be compatible with the fluid being conveyed.
• Pressure – published hose working pressure must equal or exceed the normal system pressure, including pressure spikes.
• Ends – identify the termination and threads needed for the system to define the proper couplings and adapters.
• Delivery – determine the hose size needed to deliver the required fluid volume without losing pressure or adding unnecessary weight or bulk. Also consider requirements for how the hose and/or assembly is physically provided to the end application, including date required, special packaging, labelling or certifications.
Poor system routings
Hose assembly routings are a critical component of hydraulic system performance, both in an OE application as well as when hoses are replaced. Poor routings can lead to, in the best case, an under-performing hydraulic system with less system pressure than expected. A worse case would be faulty routing leading to costly downtime, and the worst-case scenario would be an unsafe working condition. Application engineering experts can diagnose your hydraulic system and recommend routings or system changes to improve system performance, and my Gates colleagues know from experience that these consultations usually reduce hydraulic system costs, too.
The fact that hoses are flexible is a common reason a hose is chosen instead of a rigid tube, but that doesn’t mean that hoses are ultimately flexible. Common issues arise where hoses must bend – particularly bends near the coupling. Optimised hose routings will avoid hose bends near the coupling by using angled adapters, or alternative coupling options, to alleviate hose flex requirements. If a bend radius is below the recommendation for that particular hose, get creative with angled adapters and/or revisit your coupling selection to avoid sharp bends.
Proper routings also mitigate hose abrasion, whether against other hoses or against machine components, which also extends system life and minimises the risk of premature failures. Return lines are another component of the hydraulic system where we often see problems – although these lines are typically low pressure, they are a necessary component to return fluid to a reservoir, but they are often the last component considered when designing a system. To mitigate the risks of challenging routings, consider a flexible, corrugated hose design that has a tighter minimum bend radius, like Gates Multi Master GMV MegaFlex.
Finally, hose routings can minimise the likelihood of leaks in a hydraulic system with proper termination selection. Always avoid stacking adapters to both minimise system cost and the risk of system leaks. To further demonstrate the value in optimised system routings, the product application engineers at Gates provided case studies to illustrate these points. In this first example, the customer asked for Gates’ help because they were having difficulty routing hoses through a channel in the Rear Drive. Upon further inspection, Gates engineers found a few opportunities:
What Gates Engineers Observed Optimised Solution
Tee grouping created challenges routing hoses through the channel Replace Tees with a manifold.
Manifold design provided fixed points of reference for routing and improved aesthetics on the machine, plus they eliminate abrasion concerns from bundled tees.
Bundled Tees were creating abrasion concerns
4+ connections at the same point were difficult to install. Gates QuickLok connections minimise leaks and enable fast and easy assembly.
The before-and-after photos (3 and 4) show a cleaner system with improved performance and fewer leak points.
Forgetting about safety
Mistakes with high-pressure hydraulics can lead to critical injuries or even death. Here are some critical safety reminders about hydraulic systems and hydraulic hose assemblies:
1. Never touch a pressurised hydraulic hose. Rubbing your hand along a hose as a leak-detection technique, for instance, is just asking for trouble.
2. Similar to electrical systems, hydraulic systems can be energised even when the system appears to be in the ‘off’ setting. Therefore, always de-pressurise a hydraulic system prior to handling or replacing any system components.
3. When replacing a hydraulic assembly, always ensure the replacement assembly can meet the system performance requirements, including working pressure, temperature and fluid being conveyed.
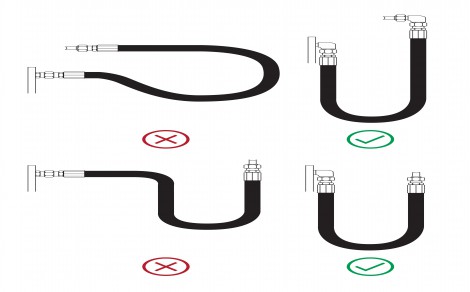
4. For hydraulic hand tools, never carry the hand tool by the hose. This can lead to pinching and pinholes.
5. For line-of-sight hydraulic lines where an operator is working near the pressurised hydraulic assembly, line-of-sight sleeving should be used to protect the operator in the case of hose or assembly failures.
Ignoring signs of wear
Hydraulic assembly inspection should be included in any system preventive maintenance schedule. These inspections should monitor hydraulic assemblies for signs of wear, including cover damage like cracking and abrasion. Ideally, the system design would reduce the likelihood of damage, but when this damage is found to reach the hose reinforcement, the assembly must be replaced.
Cover cracks can be caused by several issues. Exposure to extreme heat, particularly in engine compartments, can cause the exterior cover of the hose to become brittle and crack. Exposure to ozone, either from the sun or from high electrical charges, such as in welding equipment applications, can cause micro-cracks to appear on the surface of the hose. This is similar to ‘weathering’ that is seen in the sidewalls of tires. Ozone damage is typically seen first on the exterior of hose bends where the rubber compounds see their highest stresses. Once these cracks reach the hose reinforcement, the reinforcement is compromised because of potential damage due to moisture and debris. This damage can be mitigated by protecting hoses from high-electrical exposure and by choosing hoses with materials that are resistant to ozone.
Cover abrasion is a constant challenge – particularly in congested hydraulic systems where it is challenging to isolate one hose from others or the machine frame in dynamic applications. The most obvious way to mitigate abrasion damage is to choose hose covers that are specially formulated with abrasion resistance. Specialised nitrile rubber compounds offer a mid-grade level of abrasion resistance, and extreme resistance to abrasion can be realised with a hose cover made of ultra-high molecular weight polyethylene film. It is also possible to assemble the hose in an abrasion-resistant sleeve or hose guard, but this option considerably increases the assembly costs and can complicate hose installation in the application. In addition to selecting abrasion-resistant hose covers or accessories, the hose routing can also have an impact on hose abrasion. Use clamps to support long hose runs or to keep hoses away from moving parts, taking special care to allow for volumetric expansion. Hoses that bend around a portion of the machine frame should be assembled with enough length to avoid rubbing over a machine corner. And it’s worth noting that hoses should never be clamped to the machine frame, which could restrict expansion in the curves when the hose is pressurised.
Proper assembly
A user can procure the most premium and highest performing hoses and couplings in the world, but if they’re not assembled correctly then they’ll never realise the value. Proper assembly has several components – qualified hose-coupling interface, assembled by a trained technician, and with a verified crimp diameter.
By qualified hose-coupling interface I mean that the specific hose and specific coupling are verified to work together. The verification is more than just crimping to a certain crimp diameter – it should be verified by burst and impulse testing across a range of crimp diameters to account for hose and coupling manufacturing variation as well as crimper and die tolerances. The testing should mimic the intended application, particularly the temperature. A hose-coupling interface may work well at standard 100degC operations and then not perform at all at elevated temperatures above 120degC. Further, hoses are not all the same. Even though hoses from different manufacturers may meet the same performance criteria, the properties of the compound affect the robustness of the hose-coupling interface.
The thickness of the rubber materials and the placement of the reinforcement material can change the crimp dimensions as well. Likewise, couplings from different manufacturers are not necessarily equivalent. They may be made from different grades of steel, different material hardness, and include features, such as serrations, that are dimensionally different, significantly impacting the quality of the hose-coupling interface. Even the radius or heights of these features can significantly impact assembly performance.
A trained assembly technician is also critical to the assembly process. She or he must be trained to select the proper hose and couplings, cut the hose to the right length, remove debris and contaminants from the inside of the hose, ensure full coupling insertion onto the hose, select the appropriate crimper setting, and place the assembly properly in the crimper dies… and they must do all of this safely.
Finally, after the assembly has been made, the crimp diameter on each end of the assembly must be verified for proper crimping. This measurement is often performed with calipers and compared to a qualified crimp diameter range. Some systems also use a go-no go gauge to verify the crimp by reviewing either the crimp diameter or the stem collapse.
Smart crimpers are gaining popularity in the market. These crimpers make operator training and quality assembly easier by mistake-proofing various steps in the assembly process. Smart crimpers, such as Gates GC20 Cortex crimper, typically include the crimp settings in an on-board computer to eliminate the need to reference the crimp setting and program the crimper.
While it takes years to become a hydraulics expert, attention to several important details can mitigate many hydraulic system errors, avoiding potentially expensive – or worse, dangerous – fluid power faux pas.
https://www.linkedin.com/company/gates-corporation/
https://twitter.com/gatesindustrial
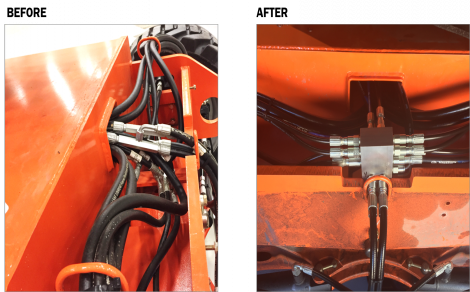
-
PPMA 2025
23 September, 2025, 9:30 - 25 September, 2025, 16:00
NEC, Birmingham UK -
Advanced Engineering Show 2025
29 October, 2025, 9:00 - 30 October, 2025, 16:00
NEC, Birmingham UK