Boardroom Report - Challenges and opportunities
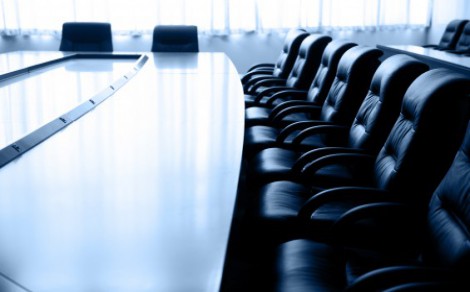
Hydraulics & Pneumatics spoke with leading solutions providers and industry associations about the current state of play within the fluid power and related technology space.
This is a very important time for the hydraulic sector, and innovation is focusing more and more on the connectivity of the products with sensor devices and external devices apps, wi-fi, etc. This is one of the predominant observations of Francesco Chessari, executive director, MP Filtri UK Ltd, who points out that more and more users want to be able to check their hydraulic system from any remote area they may be in and to be able to check all their sensors with a push of button.
Chris Buxton, CEO, the British Fluid Power Association (BFPA), also recognises the importance of connectivity and, moreover, points to a related inexorable trend that has been accelerating over the past ten years – the convergence of technologies. “In order to grow, companies more used to capitalising upon a niche market will have to consider diversification and solution sales,” he says. “Customers no longer want a hydraulic technician or an electrical engineer or a pneumatics technician – they want a systems engineer who can take a holistic view of their requirements and can deliver a range of integrated products that meet that requirement. The future is integrated systems and those who keep hankering after the past and trying to tell us to ‘go back to our roots’ and ‘concentrate upon what we know’ are like King Canute on the shore trying to stop the tide. They will surely drown and go out of business. We need to embrace and exploit the change – not fight it.”
Maturity
However, Buxton believes that the fluid power market is mature and, to a degree, has become a little complacent. “For some years, the market has relied upon the fact that it has a fairly unique position with few alternative preferable technologies being available for its various applications,” he says. “As new technology emerges, many of the alternatives are now beginning to become credible and some would argue that they are more environmentally friendly. For some years, there has been a trend to move away from fluid power to electromechanical (EM) technology, particularly in the applications where power density is not relevant. With progress being made in control techniques both in DC and now AC drives, that threat has become all the greater. The industry used to suffer, and still does to some extent, from an image of being dirty and wasteful in terms of energy consumption. There has been a lot of work undertaken by technical experts who understand the detail of the technology of fluid power in conjunction with other bodies, like IMechE, to increase the awareness in the industry of how to overcome these issues. This has been done and continues to need to be undertaken at a grass roots level.”
Buxton therefore maintains that the primary trends in this sector are:
• The trend towards systems solutions and maintenance. Buxton believes there is a need to encompass control of systems as an integral element of the industry. Competition from the electromechanical industry has shown that companies deliver complete drive systems and not just the ‘fluid’ elements,” he says.
• Greater use of pneumatics and electromechanical drives in place of hydraulics – (especially in clean environment sectors such as food and electronics)
• Linear drive technology is growing particularly fast
• Increasing use of automation and robotics
• Shift towards general ‘motion control technology’
• Fluids in use in hydraulics have been developed for use in sensitive environmental areas such as subsea. Buxton points out that the bulk of systems however still use mineral oils. “Companies are now claiming developments to lower friction in automotive oils and synthetic oils provide longer life for a larger initial investment,” he says.
Buxton continues: “As the trade association responsible for this sector, the BFPA needs to respond to these trends and, equally importantly, help the membership to follow suite. There is also growing acceptance of the fact that there exist a number of challenges both in terms of required research and market education.” According to Buxton, the research challenges are: Increasing the energy efficiency of fluid power components and systems; improving and applying energy storage capabilities; and reducing the size of fluid power components and systems. The market education challenges, states Buxton, are: Building ‘smart’ components and systems; improving the reliability of fluid power components and systems; and reducing the environmental impact of fluid power components and systems.
Vanda Jones, executive director, British Compressed Air Society (BCAS), explains that BCAS industry statistics are always an excellent barometer of industry performance and an indicator of any shift in demand for particular products or services. “They use order volumes for our manufacturing sector and revenue figures for our service delivery sector, to provide an instant indicator of where the broader economy is heading,” she explains. Jones adds that, due to the coronavirus pandemic, the initial sharp downturn in the equipment orders is unsurprising, as is the fact that the service sector suffered less. “The compressed air industry did not stop working during the crisis,” she points out. “Key sectors still needed service support to help keep industries including, utilities, food and beverage as well as manufacturing working safely.”
Rob Bartlett, director and CEO of the British Valve and Actuator Association (BVAA), reflects that a key focus at the moment is what the year 2021 holds for the industry. “2020 was severely dented, but on the whole survivable in business terms,” he says. “We hope for normalcy next year, but the ‘mood music’ at the moment isn’t great and there’s a feeling 2021 might actually be the poorer year.” With reference to the pandemic, Chessari comments that in many countries MP Filtri has seen a shortfall in business, while it remains strong in domestic and export markets.
Ongoing product development
In terms of product development within the vendor community during 2020, Stefan Gunter, sales and marketing director, Abdex Hose and Couplings Ltd, says suppliers to Abdex, such as Uniflex and Parker Polyflex, have been active bringing new products to market. “For example, Uniflex has brought new state-of-the-art hose cutting and crimping products to market to suit different types and sizes of hydraulic hoses,” he says. “Parker Polyflex, another key supplier within our portfolio, has also launched some innovative new lines, including PFX3010-5; a new range of 3010 bar hoses that will rationalise some of the previous lines in the portfolio, developed for ultra-high-pressure applications. These hoses combine excellent handling and long service life with very good safety standards. They are suitable for working pressures up to 301 MPa.
From a business perspective during 2020, Gunter explains that Abdex experienced a slowdown of around 20 to 25% following the first UK lockdown period, although this quickly bounced back going into June and towards the end of the year, “Some key customers furloughed staff and this resulted in some of our regular contacts not being available,” explains Gunter. “A few customers also tried to cut out the distribution arm and go directly to the manufacturer for certain products in order to save money, we are lucky that none of our business partners would encourage this even in a difficult market. Some also wanted to look for sources of cheaper products. However, of course, cheaper often means more inferior. So, we discussed these issues with the companies concerned, emphasising that cheaper products don’t guarantee the same levels of reliability, longevity and safety. Also, with regard to distribution they came to appreciate that they could miss out on the all-important testing and dedicated aftersales service and support that we provide. We won most of them round in the end on this basis.”
Martin Cuthbert, managing director, Webtec Products Ltd, considers that the pandemic has accelerated the move towards digitisation. “We all see that with the use of video conferencing, but the pandemic also has accelerated the discussions around predictive maintenance since current difficulties in being able to travel are now hindering the ability to service machines when they breakdown and thereby increasing the cost of a breakdown,” he says. “I think this is leading more companies to consider alternatives, such as using technology to measure system performance and try and predict failures before they happen. Webtec is active in this field and has many customers using our hydraulic measurement equipment for reactive, preventative and predictive maintenance. We are also involved in various projects to develop rugged products for permanent installation on online machines. Webtec is just publishing a training video, written by Steve Skinner for Webtec, explaining the benefits of the different maintenance approaches that could be of interest to readers. I think it only makes sense; the companies will increasingly want to be forewarned and forearmed to carry out service, especially as the cost of downtime continues to increase.”
Chris Ringlstetter, president, ELGi Europe, considers that the buzz in the compressed air industry at the moment is the Internet of Things (IoT), which, as he explains, is all about collecting mass data allowing the integration of digital platforms into industrial processes and machines that improve energy efficiency, reliability, and control. “For example, coming in early 2021, ELGi’s ‘Air Alert’ is an IoT-enabling device which, when fitted to a compressor, allows for remote monitoring of data, and provides meaningful insights for the customer on aspects of the compressor’s running such as service intervals, energy efficiency, changes in air consumption, and general compressor health,” says Ringlstetter. “This service provides real-time monitoring of compressor efficiency, predictive maintenance to avoid costly down-time, and insights into operating conditions that help product development teams make improvements to connected equipment.
Digitalisation
Andy Parker-Bates, product marketing manager, Festo UK, comments that over the past few years there has been much discussion around Industry 4.0 technologies and the digitalisation of manufacturing detailing how the factories of tomorrow will be seamlessly connected across their supply chains and through their processes and systems. “Customers will be able to configure their unique product and place orders directly on the factory in real-time,” he says. “Autonomous systems will then order raw materials, schedule the build, allocate resources and start the production line running. For much of the UK’s manufacturing industry, this is a utopian future which bears little resemblance to today’s factory floor. It is seen as too difficult to implement and the preserve of large multi-national corporations with huge R&D budgets. What this pandemic has shown, however, is that the principles embodied in digitalisation are more relevant now than ever before and apply equally across the whole of the manufacturing sector.
“Take the FMCG sector as an example. At the start of the pandemic in the UK, we saw supply chains disrupted, a surge in demand and empty supermarket shelves. Many manufacturers responded by reducing the number of varieties they produce to enable them to concentrate on volume production of a smaller range of products, with reduced complexity, fewer changeovers and often with reduced numbers of staff. While this produced the immediate boost the country needed, it demonstrated an inherent lack of flexibility and agility in the manufacturing sector and shows just how far we need to develop to reach the Industry 4.0 vision of the ‘factory of the future’.
“Fortunately, technological shifts already taking place within automation are offering machine builders an ever-increasing range of newer, better connected, more intelligent fluid power products. Products such as IO-link enabled sensors and valves deliver greater operating flexibility and diagnostic insights than ever before and finally bring historically ‘dumb’ field-level devices into the machine control architecture. Access to relatively basic information such as the number of switching cycles of a valve enables maintenance to be scheduled to avoid busy production runs, or manufacturing can be routed to a parallel machine to avoid potential breakdown scenarios. Similarly, an optical sensor with the ability to report the cleanliness of its lens can give advance warning of degradation before it hits production.
“Announcements of the last few weeks hopefully signal some light at the end of the tunnel with respect to COVID-19, and as manufacturers reflect on the events of the past nine months many will be concluding that a greater use of already available automation technologies within their processes could have mitigated many of the challenges that they faced in terms of staff shortages and capacity issues.”
Alexander Pavlov, general manager, Atlas Copco Compressors UK, believes these largely remain energy efficiency and connectivity, on top of reliability. “I believe these days we can also speak about the shift towards green aspects of energy efficiency rather than only financial benefits,” he says. “The latest revolutionary innovation from Atlas Copco is a new generation of oil-free screw compressors (ZR VSD+). Those new compressors consist of two drive trains – low- and high-pressure stages, where each train has a frequency inverter, PM motor and directly coupled oil-free screw element. The controller within the compressor makes sure that the two drive trains run in perfect balance and always at the most efficient operating point. This new generation delivers even more energy savings to our customers, and I am happy to confirm that some of those brand-new models are already installed and running by UK customers.”
As for connectivity, Pavlov states that this is an incredibly exciting journey the company is going through; with more than 3000 Atlas Copco compressors connected in the UK currently. “This provides an enormous amount of intelligence data on how our products are running, and we apply many AI algorithms on that data to prevent technical problems and highlight potential improvements,” he says “Recently, we also introduced a new communication device which can work with any compressor make, not only Atlas Copco units. The current pandemic highlighted the importance of remote connectivity solutions, and we also experienced more high-speed track projects where the time between RFQ and commissioning was incredibly short, for medical and PPE sectors for example.”
Brexit
How is Brexit impacting on the fluid power equipment and systems marketplace? Buxton believes the fact that the EU–UK Trade and Cooperation Agreement (TCA) was announced at such a late stage did little to help companies trying to prepare for the end of the transition period – especially against a backdrop of the COVID-19 Pandemic. “We were all expecting a ‘skinny deal’ but when it was announced it was certainly short on detail in many areas,” he says. “In fairness, such areas tended to be in the financial and general services sectors rather than in the area of goods, which will have the greatest impact upon the fluid power sector. However, I feel that it was somewhat disingenuous to announce the deal as being ‘tariff-free’ as the rather obvious and understated caveat to this was the fact that goods are only tariff-free if they meet the necessary rules of origin, and most of the confusion that has since arisen revolves around the disproportionate complexity of these rules.”
Buxton explains that the BFPA seeks to help members through this jungle of regulation but considers that the more one delves into the subject the more complex it becomes. “Fluid power companies, like most product-driven industries, will have to examine their supply chains to check that they meet percentage thresholds for content,” he says. “This is a non-trivial exercise, and many are having to employ expensive consultants to help them through the process. On the potential upside, we may see an increase in domestic sourcing of product as the cost of importing increases – as it surely will.”
Chessari believes that, with Brexit, we are facing increased red tape for certain products as well as increased transport costs for imports and exports. “Even with the EU zero custom duty trade deal we will still see an increase in administration costs and logistic issues,” he says. “Brexit is also creating a lot of uncertainty and this is the most difficult year to forecast. In the next 6 months I think that logistics delays will be resolved as the carrier companies become more organised with group shipments, more familiar with the new required documentation and UK exporters start using new software (like CHIPS) to deal with customs directly without paying this charge to the transporter. Brexit will have increased costs for UK businesses and the only options for the next 2 to 3 years will be to either absorb the cost or to transfer it to the EU customers. In the long-term Brexit could be successful only if the UK manages to negotiate good deal with non-EU countries.”
In terms of the Brexit outcome uncertainty during 2020, Gunter explains that Abdex increased its stock inventory by around 40% to ensure its customers would not experience any slowdown in supply within the UK. Some suppliers in Europe and the US were naturally concerned by the pandemic and their ability to work as normal. In the event, they operated very efficiently under the circumstances. Nevertheless, we felt the best thing for us to do was to boost stock to protect the needs of our customers just in case there were any supply issues further down the line, whether due to a bad Brexit outcome, the effects of the pandemic, or both.”
Martin Cuthbert comments that Webtec recognised the threat that Brexit would have on its business as soon as the Referendum happened in 2016. “Speaking to many of our customers in central Europe, their perception has been one of dismay and it has clearly made the UK a less attractive place to consider purchasing from as we’ve progressed through the transition period,” he says. “The European perception seems to be that buying products from the UK is going to get much more complicated and much slower and therefore potentially more expensive, due to the increased burden of buying from the UK and shipping it into mainland Europe. Whether this turns out to be true or not is probably no longer relevant despite the last-minute trade deal as the damage is already done and people’s perceptions have been reinforced reading the past four years’ news headlines – and it will take quite a long time to change them. Over the past two years Webtec has set up a new company in Germany called Webtec Europe, specifically to serve our central European customers. We have recently opened our European warehouse and we are also finalising our service capability so that our European customers no longer have to deal with a British company but can be served entirely by a German one. This approach has been welcomed by our customers as it provides certainty in a very uncertain world. Webtec Europe has also been recently accredited to ISO9001: 2015.”
Ringlstetter comments that he is happy to see that a deal has been agreed upon between the European Union and the UK, and that so far we have not experienced severe effects on the transport of our equipment into the UK. Regarding the effects on ELGi Europe’s business, Ringlstetter explains that the company is currently gaining traction in the UK & Ireland, and he anticipates this will continue throughout 2021 and beyond. “We continue to invest in this important market even during the pandemic because it’s clearly evident that there is a need for a company like ELGi in the compressed air industry.” He adds.
Adrian Farnham, managing director, Camozzi Automation Ltd, explains that amid the uncertainty around future trade agreements during 2020, Camozzi Automation, like so many businesses, was eager to start forging and implementing Brexit plans. “We substantially increased stock levels; not only of standard components, but also of kits to enable Camozzi Automation to manufacture and assemble locally in the UK,” he points out. “This also means we have to be well-versed in new articles of conformality. As we know, UKCA marking will apply to most goods currently subject to the CE legislation. The main implication during last year, which has been well-documented, was the economic unpredictability, as a result of a possible ‘No Deal’ Brexit, inevitably leading to reduced consumption and loss of revenue for manufacturers. It was a great relief to Camozzi Automation Ltd, as I am sure it was for some many UK businesses with highly integrated EU supply chains, that a UK-EU deal was stuck.”
Farnham continues: “We are all in no doubt, the ‘break’ from the EU will not be ‘plain sailing’, with potential trade complications surrounding supply chains and increased operating costs etc still remaining a challenge. UK manufacturing has been so tightly linked with the EU for so long in a number of ways. Nearly a half of UK exports and imports of manufactured goods go to, and come from, the EU. Sectors such as automotive are highly integrated into EU-wide supply chains. The fluid power market is no different, and we will have to find ways in which to pass on these additional costs.
“We are positive, though, that Brexit does open the door to new opportunities, innovation and productivity for organisations like Camozzi Automation, who are focused on delivering new technologies within the manufacturing sector, as well as increasing investment in stockholding, local manufacturing and personnel, and it’s up to us to seize on this optimism and opportunity and ensure UK manufacturing is at the forefront.”
Jones reflects that, as we get used to working in our new normal, we are refocusing on the industry’s requirements. “Despite a signed agreement, the process of bringing goods into the UK and providing service to the EU is not without its challenges,” she says. “Early issues surrounding rules of origin and tariffs will be worked through, but we should not expect this to be without financial impact. EU legislation and directives are also core to the trade association and as we move into the post EU era. It will be critically important to ensure members and users are well-informed of any changes and potential divergence in this important area.”
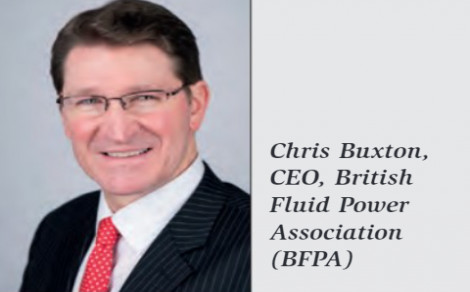
Jones adds that as well as the day-to-day standards development work, BCAS is working closely with BSI to ensure that our industry key players are well-represented at this important crossroad. “The Society is a ‘go-to’ service for standards and legislation interpretation in our sector and this new era brings with it challenges that we are ideally placed to support,” she says. “Being a member of a trade association, our members are well-placed to ensure they have the information and a source of reference and, in conjunction with BEIS, they have acknowledged the role trade associations have played in preparing their members for the transition.”
Pavlov comments that Atlas Copco Compressors UK is one of the leading providers of machinery and services to the UK manufacturing sector, with factories and distribution centre located in Belgium and Italy. “Therefore, we very much welcomed the free trade deal announced in the last days of 2020,” he says. “Since all of our products (compressors, blowers, dryers etc.) qualify for EU preferential origin we are not paying import duties, except for some spare parts sourced from outside of the EU. This is very good for our customers and for ourselves. We are also very happy to say that for our import flows we are experiencing no delays at all in European and UK ports and airfreight hubs, which is also as a result of our thorough preparation to make sure that all paperwork was correct from day one.”
Re-shoring
Some level of ‘re-shoring’ – for example, relocating production plants from Asia back to Europe or the US – has taken place. Neil Anderton, hydraulics and industrial director, Slack & Parr, explains that Slack & Parr has had a different view on the topic of re-shoring for some time. “While we did open our own workshop in China back in 2005, this was mainly for service and support,” he says. “Despite many of our peers and competitors moving out to supposed low-cost areas of the world such as China, Vietnam, Eastern Europe etc, we had always felt the potential negatives largely cancelled out the potential positives. We had spent a lot of time analysing and debating the best way forward, and in the middle of 2019 started work on our brand new, 75,000 sq ft factory right next door to our existing one in the heart of the midlands. For us, the fact we have been a UK engineering company for over 100 years is very important to us and our customers. Also, the skillset and quality of the local workforce is absolutely key to our business and how it performs. The fact that there is a lot of re-shoring happening now feels like vindication of the recent decisions we have made.”
Market climate
What are our commentators’ perceptions regarding market/economic improvements within the fluid power and related technology sectors over the past year or so? Jones makes the point that energy concerns continue to dominate the drive for ever-greater efficiency in compressed air systems. “For example, the Government’s Clean Growth Strategy for meeting the UK’s legally binding carbon commitments aims to help businesses decarbonise,” she explains. “Part of the Strategy includes the ‘Industrial Decarbonisation and Energy Efficiency Roadmap Action Plan’. The action plan will seek to reduce greenhouse gas emissions and become more energy efficient while remaining competitive during the UK’s low carbon transition. Yet, while compressed air energy consumption represents a considerable overhead for manufacturers, its performance and efficiency can often be overlooked, and improvement programmes delayed. This can be counterproductive, because there are many simple ways that users can reduce their energy usage, without investing in new capital plant and equipment. Whether its fixing leaks, recovering heat, improve control, managing air downstream, or simply encouraging staff to use compressed air more efficiently and safety – taking a whole system approach to energy savings really can pay dividends.”
Bartlett reflects that there was clearly a shock to the system in the spring of 2020, doubled down by the oil & gas sector’s volatility. “Many members did take the opportunity to re-structure their businesses accordingly,” he says. “We then saw decent rebound as the summer progressed, only to regress again in the autumn. Short-term it doesn’t seem particularly rosy, but a long-view has always paid off in the valve industry.”
Chessari considers that the biggest challenge for technology in MP Filtri’s sector is the data security. “If businesses don’t access and store technology in a secure way, this will be a concern in the year ahead,” he stresses. “There would be a huge amount of business and personal data transmitted and stored electronically. This will increase the opportunities for data breaches.” Another issue cited by Chessari will be if the pandemic continues, how to build new relationship with important potentials. “Can we do that over video-calls?” he asks.
Ringlstetter points out that the global air compressor market was estimated to be around USD 15 billion with a forecasted CAGR of between 2 and 3% year on year (pre-COVID-19). “Even though the pandemic has had a significant impact on world-wide capital investments, we are confident that a correction in the market will follow the widespread introduction of recently announced efficacious vaccines,” he says. “However, one of the silver linings to this horrendous pandemic has been the realisation that tackling climate change just might be possible. Who will ever forget the images of the ‘before and after’ shots of cities normally blanketed under a fog of pollution becoming clear again as industries and travel came to a standstill? People do not want to lose their blue skies and views of almost forgotten mountains off in the distance as they return to their hectic and wasteful past habits. Therefore, the focus on energy efficiency will play an even more important role in our recovery.”
Ringlstetter adds that while speaking with ELGi Europe’s channel partners and end users, the company is sensing an increased confidence in its ability to overcome this period of uncertainty. “Looking forward, investments in capital equipment will return, but the market will be even more demanding – specifically as it involves the lifecycle cost considerations for purchase decisions since energy consumption is by far the largest component (representing up to 63%) of running a compressor, and energy efficient compressors not only save money, but they also pollute less.”
Pavlov reflects that after an unprecedented contraction in Q2 of 2020, the market quickly recovered to pre-pandemic levels. “Currently, demand is quite strong, and the second lockdown hasn’t made much difference,” he adds.
Health & safety
Are current health & safety policies and practices adequate in our industry? Bartlett makes the point that the valves industry is particularly safety conscious in any case with an inbred safety culture. “We’ve certainly not been made aware of any major outbreaks in members’ premises,” he says. “BVAA was quick to relay the latest guidance to members at all times, and I was surprised how keenly our own office closures and openings were followed and commented upon while we endeavoured to give lead and be the proverbial ‘Goldilocks’.”
Jones explains that BCAS contributes to numerous standards and legislative bodies both in the UK and in Europe, and provides regular updates to its members and the wider industry on best practice and regulations. “For many years, BCAS has been the secretariat for many standards’ committees, producing technical standards for our industry on a broad range range of products and services,” she says. “BSI and ISO, for example, depend on industry participation to ensure these standards are balanced, workable and add value and we continue to work well with our partners towards global consolidation of standards. However, an area that concerns us is the risk of divergence in legislation and directives between the UK and the EU during the transition period. In some areas, this divergence is deliberate, such as the UK Government’s desire to provide more stretching targets for the Eco design directive than our European counterparts. In other areas, we may see a slippage in alignment. For example, the machinery directive is being reviewed in Europe currently, but this work will be concluded after the UK has left the EU, leading to, at best, a potential timing difference – or more crucially, a difference in approach and implementation. At this point in time, it is not clear how the Government intends to address this issue. However, one thing that is clear is that BCAS will continue to work diligently to identify and track these areas of concern for our members.”
One other area that has concerned BCAS during the Coronavirus pandemic is to ensure best practice guidance regarding the treatment, quality and maintenance of compressed air continues to be followed. “The BCAS technical helpline has received an increasing number of enquiries during the Coronavirus pandemic from end-users concerned that their compressed air supply is adequately protected and seeking advice to ensure that there can be no risk from airbourne contaminants,” explains Jones. “To assist, users are advised to refer to BCAS’s free guides, which can be downloaded from the website at www.bcas.org.uk, including BPG102 for compressed air purity and BPG104 for best practice advice on the filtration and drying of compressed air.”
Risk factor
Buxton believes health & safety is one of those areas where enough is never enough. “It often boils down to practicality and return on cost,” he says. “Life is risky. Where we draw the line of acceptable risk is ever changing and can take step-changes in the event of a serious and well-publicised accident. Fortunately, whilst fluid injection injuries are particularly unpleasant, the industry statistics are still good compared to many industrial sectors. However, this is not an excuse for complacency and as the Trade Association for the sector we continually strive to provide a platform for members to improve both their safety record and the training of operatives. The BFPA Hose Assembly Scheme and its associated training are a good example of this.”
Gunter explains that Abdex has joined Stichting Industriële Reiniging [Industrial Cleaning Foundation] (SIR), the organisation dedicated to promoting and regulating safe working in industrial cleaning situations in applications within the Netherlands and Belgium. SIR serves as an example of how effective self-regulation can be as regards safety in a particular sector. “For many years, Abdex has been selling product into Europe and we wanted to secure SIR certification in order to further enhance our strong portfolio,” says Gunter. “Abdex is fully certified by Parker Polyflex for HP and UHP up to 4000 bar working pressure. The company is also a member of the BFPA and the WJA, however the team recognised the importance of SIR in the European marketplace.”
As a new member, Abdex has signed the Declaration of Intent. “Standardisation, certification and safety is very important to us,” says Gunter. “Abdex will always supply our customers with 100% safe and tested hose assemblies/products. Continuous improvement, standardisation and training will ensure that the industry and those supplying it will remain a safe one. Abdex, with the help of SIR, Parker Polyflex, the contractors, the jetters and everyone in the industry can further ‘raise the bar’ and standards to make the industry more efficient and most importantly safer.”
Gunter explains that the Abdex production team will be testing and working to strict regulations (including additional exacting controls) every day. “Our equipment and procedures ensure the safety of our employees,” he says. “Stringent procedures at Abdex means our customers can be assured of the product quality and safety of every hose assembly supplied by Abdex. Abdex customers all over the world can be secure they are receiving a fully certified, 100% tested, 100% safe, asset managed and fully traceably hose assembly/product.”
Education and training
What are our commentators’ views on current available training courses and education in general within the UK? Jones maintains that ensuring engineers are equipped with the latest skills remains a key priority for all sectors of industry, in a bid to ensure that best practice, changes in legislation and standards are all adhered to. “Recognising this need for training to be delivered to suit the needs of a dynamic and changing workforce, Jones points out that BCAS has recently invested in a new e-learning portal, allowing delegates to learn at a pace, and from a location, that suits. “BCAS is recognised within the industry as a provider of training and development for engineers, technical professionals and users of compressed air,” she says. “Working with its members, the society develops training based on industry standards and best practice. These include specialist courses that are tailored to the needs of industry professionals, end users and suppliers; that combine the safe working and understanding of compressed air with its multiple uses.”
In Bartlett’s view, the flow control industry is blessed in many respects as it can rely on superb training centres and expertise. “BVAA members often comment on the quality of available talent when recruiting, however, and I still maintain that you can best invest by ‘growing your own’,” he says. “It is of no surprise to me that the companies with seemingly the best talent are the ones out there doing the hard yards at school and university jobs fairs.”
Buxton has always believed that a strong skills base and associated education system in any society is the backbone of its economic and social success. “Since the 1970s, through a mixture of pseudo-intellectualising and political intervention, the UK educational landscape has become over complex and is in many ways unfit for purpose,” he says. “This is a sweeping generalisation and there are always going to be shining examples of exceptions to this statement, but it is significant that the single biggest obstacle to business growth in the UK is a shortage of suitably qualified individuals – with a good work ethic. This latter qualification is a harsh reality and successive governments from both sides of the House have spectacularly failed to address the problem. Until we do, the UK will never reach its full potential and it is now all the more important in light of Brexit.”
The future
What do our commentators thing about the future with regard to technological enhancements/innovations in the UK over the next couple of years or so? Bartlett’s view is that materials – particularly non-metal ones – is going to be more and more important, as is inherent recyclability – something he believes the industry has often neglected. “The really exciting area for me, though, is hydrogen,” adds Bartlett. “If we are truly to transition from the steadfast reliability of carbon-based fuel, we have to make a good fist of Hydrogen – with all its challenges – and cooperation across many disciplines and industries is the only way this can happen.”
Chessari explains that MP Filtri will continue to produce the standard range, but it will have an increase percentage of bespoke products, which will be technologically based. “In order to satisfy the demand, business will try to develop products with the lasted technology, which can serve a wider range of applications,” he adds.
Anderton believes innovation is the single most important aspect of Slack & Parr’s business at the moment. “We are well aware that there are lower-cost alternatives in the market to the equipment we provide,” he says. “Customers are generally comfortable paying slightly more provided they are getting value for money and seeing the benefits that extra cost is giving them. The minute you lose sight of that as a supplier, you can guarantee your customers will also notice. Therefore, for us, constantly pushing to ensure our products are at the top of the list for quality, and constantly looking at ways we can innovate and improve our range is expected of us. This is a way of ensuring our customers are constantly receiving the return on investment they are looking for.”
Pavlov believes we will continue to witness innovations in machine drive technology, drying technology, connectivity, and visualization, along with digitalisation of business processes. “For instance, in some cases we can now do a remote audit of a compressed air system, instead of installing loggers on the machines,” he says. Pavlov adds that another trend expected to continue is the longer service intervals on new compressors, which will require less service interventions.
Ringlstetter re-emphasises the importance of IoT, the reduction of lifecycle cost and energy efficiency, but adds that we are also witnessing a rise in demand for oil-free and contaminant-free compressed air while still meeting the expectations of reduced lifecycle cost and digital (IoT) compatibility. “At ELGi, we are already providing such solutions and are particularly proud of our recently launched AB ‘always better’ compressor series, which can be considered a disruption in the existing range of oil free compressed air technologies,” he says. “ELGi’s AB portfolio offers customers a no-compromise, oil free solution at approximately 8 to 10% reduction in lifecycle costs when compared to prevailing oil free technologies. It offers significantly lower maintenance costs and improves ease of use, with unprecedented reliability and high air purity for sensitive industry applications. We have witnessed strong adoption of our AB range in the pharmaceutical industry on account of our technology’s high reliability coupled with the lowest life cycle cost in the market. In Europe’s food & beverage industry, this technology is proving its value in, for example – a winery in the South of France. This specific customer produces high-quality organic wines and therefore purchased several AB Series air compressors to ensure zero contamination during their production processes.”
Best of both worlds
With the shift away from mass production towards mass personalisation and ever smaller batch sizes, Parker-Bates comments that proponents of electric drive technology have been quick to pronounce the end of pneumatics. “With infinitely variable positioning, and the capability of being re-configured ‘on the fly’ as different product sizes, weights, or even types pass along the line; electric drives certainly appear to have an advantage over static, dedicated pneumatic systems,” he says. “However, ‘technology agnostic’ manufacturers have been working to harness the power of both electric and pneumatic technologies to develop solutions that offer the best of both worlds. While the ubiquitous pneumatic cylinder has long been the mainstay of many linear pushing or pulling applications, there are times where electric technology would be more convenient, but the cost has been prohibitive. This could perhaps be on a conveyor system where a single-track stop is required a long way from the air supply, or maybe a piece of desktop laboratory equipment which is moved regularly and where the availability of air is not guaranteed.
“New lower cost ‘pneumatic replacement’ cylinders such as Festo’s Simplified Motion System (SMS) are designed to be a drop-in replacement for just these types of applications. Utilising closed-loop stepper controls, they offer reliable end-to-end positioning with variable dynamics but at a fraction of the cost of servo drive systems and with simple IO-Link or digital control.
“In the same vein, pneumatic systems are now being equipped with the kind of flexibility that one would typically associate with electric drive systems. Increased connectivity either through Fieldbus or IO-link technologies allows many once ‘dumb’ pneumatic devices to communicate throughout the automation architecture and provide data about their performance and staus back to the higher-level controller.”
Cuthbert believes it is evident to all of us that digitisation has sped up during the pandemic. “Clearly, COVID-19 has disrupted our social lives and meant that many of us no longer meet face to face, but I feel there have been some advantages,” he says. “Webtec prides itself on its Make it Blue philosophy, a four-step approach to understanding our customers’ needs and developing a custom product offering. As part of our aim to listen to our customers’ needs, we always want to have a three-person team made up of sales, component design and hydraulic system engineering. The improvement in virtual meeting technology like MS Teams has meant that we can pull together the best group of people for the application, wherever they are in the world, to meet with the customer wherever they are and all at very short notice and in a manner that is now very widely accepted. This has the enormous advantage of improved responsiveness and better clarity of customers’ real challenges so that we can engineer the best solution for them.”
Parker-Bates believes Festo’s Motion Terminal is a good example of how intelligence was added to a ‘dumb’ valve terminal to provide a fully programmable pneumatic system. “The Motion Terminal controls not only pressures and flows but additionally the speed and operation of the connected pneumatic cylinders, while also providing a time-stamped validation of the operation performed: delivering the kind of performance that would only have been capable previously with high end, high-cost automation systems,” he explains.
Parker-Bates maintains that the digitalisation of the factory is at the heart of all innovation taking place in the fluid power industry, and the declining cost of electric motive power will inevitably lead to a gradual migration away from pneumatics to these more controllable, connected technologies in many simple applications. “However, pneumatics is fighting back with more efficient, cost-effective, intelligent and flexible products,” he adds. “So, rather than being side-lined by digitalisation, pneumatics is a technology that fits hand in glove with its electric counterparts and is key to delivering the transformation that will drive future manufacturing.”
Buxton reiterates that there will be greater use of technology that addresses the cost (both financially and environmentally) of travel; that is to say, more of what we have seen during the Pandemic – home working, communications, virtual reality for three-dimensional training etc.
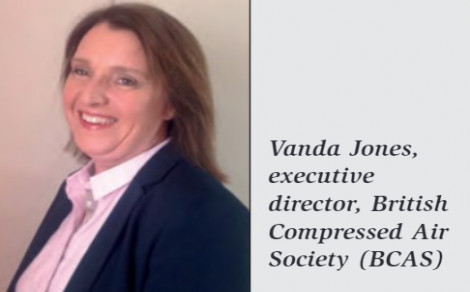
-
LAMMA Show 2025
15 January, 2025, 8:30 - 16 January, 2025, 16:30
NEC, Birmingham UK -
SOUTHERN MANUFACTURING & ELECTRONICS SHOW 2025
04 February, 2025, 9:30 - 06 February, 2025, 15:30
Farnborough International Exhibition Centre, off Aerospace Boulevard, Farnborough GU14 6TQ -
SMART Manufacturing & Engineering Week
04 - 05 June, 2025
NEC, Birmingham UK -
PPMA 2025
23 September, 2025, 9:30 - 25 September, 2025, 16:00
NEC, Birmingham UK