Achieving contaminant-free compressed air in food and beverage operations
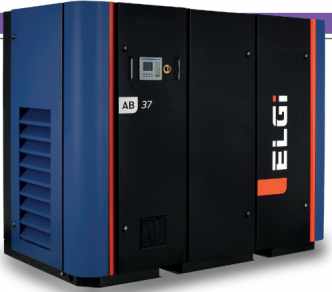
Addressing this issue, in 2018, Food Drink Europe published the ‘Toolbox for Preventing the Transfer of Undesired Mineral Oil Hydrocarbons into Food’ by the Germany Food Federation (formerly known as German Federation for Food Law and Food Science (Bund für Lebensmittelrecht und Lebensmittelkunde - BLL). This toolbox contains guidance and recommendations for the food industry in limiting contamination from various stages of food production. In relation to compressed air, this guide recommends to “check compressed air for oil penetration on a regular basis” and “use oil-free compressors, and if possible, draw in zero-emission environmental air”.
It sounds simple, but real-life food and beverage operations are anything but simple.
Filter it out
To meet such standards, in an oil-free screw compressor, an air cooler removes the heat from the compression chamber. The dry running rotors rotate at high speeds to get volumetric efficiencies injected. Timing gears synchronize rotation to ensure no contact. A separate lubrication system lubricates the timing gears. And finally, an effective sealing system prevents the entry of lubricating oil into the compression chamber.
Filtering removes much of the oil but not all of it. For example, pre-filters, high efficiency coalescing filters and activated carbon filters remove trapped oil to a great extent. But these filters themselves have characteristic limitations. For instance, above 20degC, coalescing filters do not remove fine oil vapours, leaving very fine particles of residual oil in the form of aerosols; and activated carbon filters are not usable at filtration temperatures above 40degC because the carbon then absorbs the oil vapour, gets saturated, and becomes ineffective.
Furthermore, to ensure no residual oil, air-borne particulates or vapour could enter the system, downstream air dryers and double line filters are used to further purify the air.
But filtration itself raises two more problems. First, given that approximately 10 million litres of oil have been expelled into the atmosphere over the past ten years from oil-lubricated compressors, the safe and sustainable disposal and re-use of oil continues to be a challenge. Secondly, filters create a drag on efficiency by their very function, resulting in increased energy use and running counter to the very goals of operations leaders in the food and beverage sector. For every filter that is installed in the downstream compressor line, you increase the differential pressure. This results in an increase of energy consumption of approx. 1% per filter. Furthermore, filters are often installed and paired in various combinations in the compressor room and at the point of use, resulting in additional cost and efficiency loss.
Thus, meeting these requirements for contaminant-free air in the food and beverage sector has always seemed at odds with the need to reduce the total life cycle cost.
Best of both worlds
Today, innovation and new product development has resulted in solutions that deliver ISO:8573 (P2):2007 ‘Class 0’ oil-free air to ensure that 100% contaminant-free air is produced for various applications in their manufacturing and packaging processes.
Until recently, these compressors were expensive and used primarily by large companies and those that exported their 42 HYDRAULICS & PNEUMATICS September 2020 products to markets with stringent standards (for example as set by the EU’s European Food Safety Authority). Now, technology advancement and market developments in oil-free technology and ‘Class 0’ certified compressors have changed the game and every manufacturing company can access technology that assures not only oil-free air that meets the most stringent standards, but also much higher energy savings and uptime at lower life cycle costs.
-
SMART Manufacturing & Engineering Week
04 - 05 June, 2025
NEC, Birmingham UK -
PPMA 2025
23 September, 2025, 9:30 - 25 September, 2025, 16:00
NEC, Birmingham UK -
Advanced Engineering Show 2025
29 October, 2025, 9:00 - 30 October, 2025, 16:00
NEC, Birmingham UK