- Home » Editorial » Hydraulics
Taking hydraulic hoses to the extreme
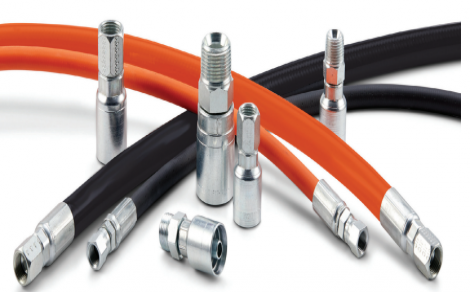
Material handling is tough, and it demands even tougher machines. Whether it’s telehandlers, concrete sprayers or aerial lifts, boom-equipped machinery takes on some of the most punishing tasks in industries worldwide. That makes robustness and flexibility absolutely crucial for the hydraulic hoses at the heart of these applications.
However, in many cases rubber hoses simply aren’t up to the challenge. Abrasion, flex fatigue, extreme temperatures and more can cause traditional hydraulic hoses to become brittle and fail prematurely – creating delays, safety risks and higher maintenance costs.
In response, thermoplastic hoses have become a more common sight in the toughest material handling machinery. Built using a variety of alternative tubing materials, such as nylon, polyester and polyurethane, these hoses offer considerable performance advantages over their rubber cousins.
Performance under pressure
The no-nonsense durability of thermoplastic hoses makes them ideal for the most demanding material handling applications. Compared with rubber alternatives, they boast far greater resistance to abrasion, chemicals, UV light, temperature extremes and other adverse conditions, as well as the ability to withstand the powerful pressure changes in heavy lifting applications while remaining flexible.
Thermoplastic hoses bring design benefits too. Installation is made easier thanks to the ability to custom thermoform hoses to fit into specific designs – enabling tighter routing, faster installation and optimised performance.
The unique properties of thermoplastic hoses also mean they can be manufactured in longer lengths than rubber alternatives. Hoses can be permanently joined together too, forming flat, compact and flexible multi-lines that can be reeled in easily.
With thermoplastic hoses weighing about 50% less than rubber wire braided equivalents, they also reduce machine weight, power requirements and fuel consumption – unleashing greater day-today value for users. Thermoplastic hoses won’t degrade like rubber alternatives either, helping to maintain a clean hydraulic system and avoiding the downtime caused by contaminated filters and valves.
All these features translate into tangible, real-world advantages for end users – such as more uptime, higher productivity, greater design freedom and considerable cost savings.
Going to extremes
Eaton’s new Synflex Optimum range is pushing the potential of thermoplastic hoses even further. The company’s new hose composition combines the temperature tolerance and flexibility of polyester-lined hoses with the chemical compatibility of nylon-lined ones. The result is exceptional reliability and versatility in even the toughest conditions.
Our hoses are ideal for heavy lifting and handling equipment. We have options for working pressures from 70 bar to 350 bar, plus non-conductive variants to support the rapidly growing electrohydraulic market. Our new materials also offer improved hose functionality over a wider temperature range from -40degC to 100degC, as well as a 10% increase in abrasion resistance.
While more robust hydraulic hoses are great news for the material handling sector, Eaton also hopes the flexibility benefits of Synflex Optimum will pay dividends for the designers working on tomorrow’s machines. When a designer asks ‘would this work?’, we want Synflex Optimum to give them the confidence that it can. We want them to be able to focus on design possibilities, not hose limitations.
Achieving this wasn’t just a question of developing hoses that can work harder and last longer. Lighter, thinner and more flexible hoses, combined with our custom thermoforming capabilities, mean machine builders aren’t held back. Our new hose covers were speciallyformulated to require 50% less routing force, reducing the chance of kinking during installation. Ultimately, these features mean designers can create highly differentiated platforms that bring even greater value to their customers.
This same mindset is also visible in Eaton’s approach to the Synflex portfolio as a whole, which has been considerably streamlined to make it easier to find the right solution for any application.
Engineered as a system
Unlike manufacturers that only produce either hoses or fittings, Eaton has taken a system-engineered approach with Synflex Optimum to ensure a long hose lifetime and minimize equipment failure.
Even with the highest performing hoses, any hydraulic system will only be as good as its fittings. In response to this dilemma, Eaton created its new 4T series. Designed to complement and support the capabilities of Synflex Optimum hoses, these fittings enable the creation of highquality assemblies with exceptional performance. Pairing with the entire Synflex Optimum range, as well as most existing Synflex hoses, these fittings also take the guesswork out of design compatibility – reducing inventory needs and simplifying machine maintenance.
Eaton’s 4T fittings feature a compact design and smaller profile too, enabling easier routing and machine assembly. “Our fittings follow a simple one-piece design to reduce matching errors and assembly time, while also eliminating brazing failure risks. A captive nut helps eliminate the weak spots found in other fittings and can increase safety in applications with high levels of vibration, as well as prevent cracks and leaks that lead to unplanned downtime. The 4T series also comes with Eaton’s proprietary Dura-Kote plating as standard, which delivers up to an impressive 1000 hours of corrosion resistance.
Ultimately, our new Synflex Optimum portfolio is greater than the sum of its parts. When used as a system, our hoses and fittings empower OEMs to reimagine machine design and break through traditional limitations.
Rubber hits the road
Maximising uptime and productivity for mission-critical systems can never be a bad thing. As such, many in the material handling space will now be looking hard at the potential of thermoplastic hoses.
No one should be afraid to dive in: If you’re an OEM or distributor, it’s time to explore what thermoplastic hoses can do for your customers, and there’s plenty of help on hand if you need it. Our own value-added services span design consulting and technical support, so we’re in a great position to assist you in developing more efficient, safe and productive systems – no matter where you are in the world.
-
SMART Manufacturing & Engineering Week
04 - 05 June, 2025
NEC, Birmingham UK -
PPMA 2025
23 September, 2025, 9:30 - 25 September, 2025, 16:00
NEC, Birmingham UK -
Advanced Engineering Show 2025
29 October, 2025, 9:00 - 30 October, 2025, 16:00
NEC, Birmingham UK