Hydraulic fluids: Understanding the value high-quality zinc-based fluids can bring to operational productivity
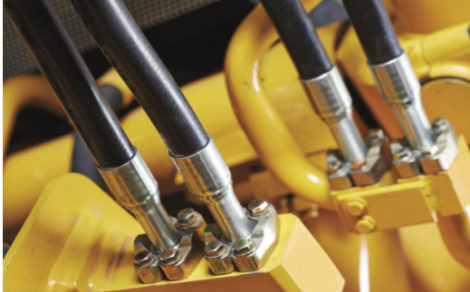
By Emma Mallinson, hydraulics global product marketing manager, Shell.
The ongoing COVID-19 pandemic has been a tale of two sides for businesses across the hydraulics industry. While some companies faced a reduction in demand, and therefore operations, over 30% of British Fluid Power Association (BFPA) members have been involved in supplying equipment (including ventilators and PPE) to the NHS as part of the UK’s COVID-19 response, suggesting that others have faced a surge in outputs [1].
Whether the pandemic has accelerated production, or operations are scaling up once again as we enter the recovery phase, businesses across the industry need to ensure that their hydraulic equipment can work harder, and for longer. Increased outputs can place additional stress on hydraulic systems by creating hostile operating conditions through higher temperatures and pressures. When coupled with increasingly compact mobile hydraulic systems, with smaller oil reservoirs that restrict heat dispersion, increased peak oil temperatures and reduced fluid residence time, it can lead to damaging oxidation, sludge and varnish formation.
Ultimately, if not managed effectively, it is a recipe for hydraulic system failure. Operators must ensure that their hydraulic systems are ready to face the challenge of ramping up or restarting operations to help minimise equipment downtime and reduce Total Cost of Ownership (TCO). Given the turbulent economic conditions we are currently facing, there is little margin for error when it comes to efficiency and productivity. Investing in the right products for the right applications plays an important role in helping to ensure consistency of output, while mitigating the risk of delays and unplanned maintenance costs.
Why preventative maintenance matters
Protecting the hydraulic system against potential issues before they become a problem is essential to achieving productive and uninterrupted operations. This is why guarding against sludge and varnish build up – caused by the oxidisation and thermal degradation of oils – is such an important aspect of equipment maintenance. If left untreated, equipment failures can then occur from reduction of the spool-to-bore clearances in valves – leading to valve malfunction, the clogging of a suction strainer that will lead to pump failure, or damage to seals and O-rings leading to oil leaks and cylinder problems. These issues can result in increased equipment repair and replacement costs, which not only inhibit uptime but increase TCO. Therefore, this is something operators need to proactively avoid.
Simply waiting for a build-up of sludge and varnish deposits in the hydraulic system to arise can have potentially problematic implications. Being mindful of the bottom line, operators should prevent and tackle deposit formations at their source – hydraulic fluids. In order to do this effectively, it’s essential that operators have a clear picture of what is available in the market to ensure that they are using oils which leverage the latest technologies and help boost the productivity, cleanliness and lifespan of their hydraulic equipment. There are a wide variety of tests on the market that allow manufacturers to examine every aspect of a hydraulic fluid, from thermal stability to oxidation and yellow metal protection.
Dispelling the zinc myth and unlocking new potential
Although most hydraulic oils sold today are zincbased, some equipment manufacturers still believe hydraulic oils with zinc technology can lead to increased sludge, varnish, shorter oil life and the associated maintenance costs from plugged valves and filters.
However, when you compare the criterion of laboratory tests for zincbased hydraulic oils against the indicators of a poor-quality hydraulic fluid (oxidation in the presence of yellow metals, thermal instability and water and air contamination), and a high-quality hydraulic fluid (excellent thermal and oxidation stability) it is evident that these poor hydraulic oil test results aren’t reflective of zinc’s properties, but those of a poor-quality hydraulic fluid.
In our latest whitepaper, ‘Are sludge and varnish killing your productivity?’, we explore how zinc-based technology in a high-quality hydraulic oil can in fact help to extend oil and equipment life and generate efficiency-based savings.
For example, Shell Tellus S4 VE hydraulic fluid features low sludgeforming technology with wear and oxidation protection, meaning that it not only produces 15 times less sludge and four times less varnish than competitor mineral based oils during high-temperature Indiana Standard Oxidation Test (ISOT) testing [2] [3], but it exceeds the Bosch Rexroth A2F10 piston pump test limit by four times [2] [4].
Significantly enhanced oxidation resistance is another benefit of highquality zinc-based oils - a factor that plays a pivotal role in equipment service life. Consequently, Shell Tellus S4 VE was shown to last at least twice as long as competitor mineral oil in industry-standard oxidation tests [2] [5]. The oil also passed the Bosch Rexroth A2F10 piston pump test (JCMAS P 045), which evaluates oxidation stability in construction applications. To pass the test an oil’s viscosity change, acid number increase and sludge build up must remain the same, within the test’s limits. Shell Tellus S4 VE remained the same for 2400 hours, which is within the test’s limits. This strong oxidation resistance evidences the tangible impact high-quality hydraulic fluid can have on operational performance.
Now is the time to take action
By helping to limit the build-up of sludge and varnish deposits, high-quality zinc-based hydraulic fluids, like Shell Tellus S4 VE, not only mitigate the risk of unplanned downtime by preventing equipment overheating and valve and filter blockages, but help to extend oil and pump life and increase productivity by up to 6% compared with mineral oils [2] [6].
We are in a period of economic uncertainty and as such, improving TCO will likely be a priority for operators across the industry. With this in mind, it is crucial to dispel the myth surrounding zinc-based hydraulic fluids and focus on the determinants of a high and low-quality oil. Whether it’s through extended equipment and oil life or productivity increase, the benefits of using high-quality zinc-based hydraulic fluids to help avoid the build-up of sludge and varnish can make a significant difference at a time when businesses need it most.
www.shell.com
References [1] https://bfpa.co.uk/news/bfpa-members-support-the-nhs-during-the-covid19-pandemic/ [date accessed: 08.07.20] [2] Shell Lubricants ‘Are sludge and varnish killing your productivity? Could the latest oil technology give you cleaner, longer-lasting and more productive Hydraulic Systems?’ whitepaper. [3] High-temperature Indiana stirring oxidation test (ISOT) JIS K2514. This test is typically a compressor oil test and favours zinc-free chemistry. However, it is a good indicator of sludge and varnish tendency. The test promotes the oxidation of the lubricant by blowing dry air in the presence of heat (165.5degC), and metal catalysts (copper and iron coils). After 48 and 96 test hours, the used oil samples were forced through a paper filter to examine the sludge build-up. [4] Bosch Rexroth A2F10 piston pump test evaluates the oxidation stability of hydraulic fluid under high-pressure, dynamic conditions in situ. The test is part of JCMAS P 045. The oil temperature in the oil tank is 80degC and 1 L/h of air is supplied to the inlet pipe to cause cavitation in the pump. The JCMAS specification for change of viscosity and acid number and sludge is 500 h but the OEM requirement is 1000 h. [5] 6400 mL of each oil was kept at 195degC. Two samples per oil were used. Steel spindles were weighed and their masses were recorded. One steel
-
Farnborough International Airshow
22 - 26 July, 2024
Farnborough International Exhibition & Conference Centre