- Home » Editorial » Hydraulics
Pump energy efficiency and risk mitigation
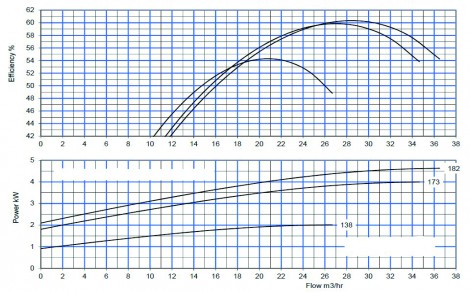
The other major consideration is how to prevent leakage along the shaft into the product or bearings. Although gland packing is still the preferred option for certain applications when the pump is handling solids, mechanical seals are normally standard. The variety and combination of materials and arrangements make them ideal for both clean and solids handling applications.
The introduction of cartridge seals made life easier by the end user not having to dismantle, re-assemble and re-set the mechanical seal each time the pump was overhauled. When quoting the manufacturer will recommend which ‘piping plan’ to use for flushing the seal. The purpose of the ‘plan’ is to create the best working environment for the seal. These plans, of which are more than 70 covering many arrangements, were originally prepared by the American Petroleum Institute (AP1). Two of the more common are ‘API Plan 11 single seal – internal flush’ and API Plan 53A – dual seals, pressurised external reservoir pressurised liquid barrier’. Dual seals are now the norm for most solids handling applications. In the past the barrier fluid was water which was simply allowed to drain. Nowadays a self-contained ‘seal support’ system is the norm. Sealless magnetic drive pumps are a good option for liquids which solidify on contact with the atmosphere (e.g. sodium hydroxide), acids or valuable liquids (e.g. demineralised water) where leakage cannot be tolerated.
Whilst pump type, materials and construction are driven by understanding the process and having full details of the conditions of service there are other areas to consider when selecting a pump to deliver long term reliability and cost savings. The most important is the bearing arrangement and the method of lubricating the bearings. A ‘heavy duty’ combination of a roller bearing at the pump end and a back to back pair of angular contact bearings at the drive end is designed to deliver bearing life well in excess of that specified by industry standards. The bearings can be grease or oil lubricated depending on the end user’s preference.
Whole life costing should be the driver rather than initial purchase price. Why, because lowest initial cost does not always represent best long-term value for money. You need to consider running costs, cost of spares, mean time between repair over time. Equally the supply chain will have an effect, availability of spares and lead time for repairs will dictate if you should mitigate potential issues by having critical spares to hand. Again, this drives you towards a more standardised strategic standard for your pumps.
OK so you have your pump, your review has made sure it is fit for role, time now for the installation. It is usually worthwhile to get professional pump installation in order to ensure you are not having to replace due to alignment issues. While pumps are aligned at the manufacturer they must always be checked after installation both with pipework loose and with pipework connected. Please make sure that your pumps have not become pipe supports! It is always recommended that a suction compound gauge and discharge pressure gauge be fitted to the pump or in the adjacent suction and discharge pipework so ‘actual’ performance can be compared against ‘quoted’ performance and any problems identified and resolved. Keeping the plants pumps optimised through Planned Preventative Maintenance now comes to the fore.

-
SMART Manufacturing & Engineering Week
04 - 05 June, 2025
NEC, Birmingham UK -
PPMA 2025
23 September, 2025, 9:30 - 25 September, 2025, 16:00
NEC, Birmingham UK -
Advanced Engineering Show 2025
29 October, 2025, 9:00 - 30 October, 2025, 16:00
NEC, Birmingham UK