A focus on energy efficiency
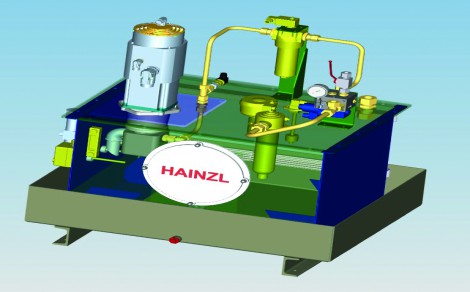
Kollmorgen has developed a ready-made drive solution for hydraulics applications for the S700 series’ servo drives. The new technology improves the energy efficiency of applications that need the high-power density associated with hydraulics. Two other benefits are control precision and longevity.
The pressure and volume flow control for hydraulic applications is generally achieved with the help of variable displacement pumps. Standard solutions use comparatively primitive asynchronous motors for this, which drive the variable displacement pumps. A control system responsible for ensuring compliance with setpoints, is connected to this arrangement. This classic setup is controlled via pressure sensors and by controlling pressure levels and flow speeds within broadly defined - and therefore imprecise - control ranges. Energy efficiency and noise emissions are two further disadvantages as asynchronous machines generate a lot of reactive power and more noise compared with synchronous motors.
By contrast, the Kollmorgen solution copes with the varying pressure and flow rate requirements associated with hydraulic applications thanks to the speed of the synchronous servo motor—so not by means of valves. The S700 servo drive assumes control of the two parameters in conjunction with the synchronous servo motor and a fixed displacement pump. It delivers the same volume with each rotation. As a result, the reference variable for control purposes becomes speed alone.
Independent pressure control in the servo drive
The setup associated with this servo drive solution devised for hydraulics applications envisages that the S700 intelligent servo inverter will assume control on a self-sufficient basis. The control system connected via field bus or analog signal only specifies the values for pressure and volume, with the servo drive then ensuring precise compliance with these through the speed. "With a sampling rate of 16 kHz, we are able to achieve fast and precise control of speeds, which gives ideal values for pressure and volume purposes," explains Kollmorgen development engineer Georg Jaskowski. The software in the S700 servo drive from Kollmorgen also opens the possibility of efficiency compensation due to higher pump speeds. "The same applies to linear interpolations, with the effect being to even out and therefore absorb vibrations and pulsations to great effect," points out Georg Jaskowski. Another benefit is the option, in actual practice, to save target pressure and volume levels via profiles or ramps in the drive in the form of prescriptions and make these immediately accessible and available to the control system.
The various benefits outlined above are used by the Austrian company Hainzl to engineer complete hydraulics solutions in the low-to-medium power range—for tasks ranging from plastics processing to handling technology. According to Peter Schrenk, head of fluids technology at Hainzl, the benefits of electro hydraulics really come into their own in the 1 to 20 kW range. As well as this, a case can still be made for centralized systems.
This technology soon pays for itself
Based on the experience of the fluids specialists from Linz, the additional costs of a servo pump, compared with conventional technology, soon pay for themselves. "We have fewer control elements in the system, and this allows us to reduce the level of complexity," said Schrenk. This technology also offers good workplace ergonomics thanks to the quieter drives used and by keeping noise emissions under 75 dB. "Noise is becoming an increasingly important issue in terms of health and safety at production firms."
The main benefits of so-called electro hydraulics are the diverse range of possible uses, with no need to settle for less (in terms of whether the hydraulics within a process area are provided by a central unit). "We are making the high power density associated with hydraulics more readily available," emphasised Schrenk. Cables are also easier to lay than the pressure lines used for hydraulics. In addition, the compact units work with far less hydraulic oil and are only in active operation when the connected process actually requires hydraulic power too. By contrast, centralised systems always need to maintain operating pressure – particularly in production processes where hydraulic axes are working as a group with time delays involved. Thanks to the highly dynamic servo motor from the Kollmorgen AKM series, however, electro hydraulics are immediately operational from a standing start.
Over the long term, this setup translates into improved energy efficiency as losses in standby mode are no longer an issue. This goes hand in hand with a longer service life for the hydraulic medium as the oil ages more slowly due to a reduction in mechanical stress. The benefits are: Lower costs in terms of operating materials and improved availability thanks to longer maintenance intervals. The extended service life of the fluid, due to the targeted use of hydraulics, also avoids any excessive increase in ambient temperature—through an overall reduction in power loss. And any reduction in "waste heat" is good news for OEMs and machinery operators, who will have less to worry about in terms of controlling or reducing rising temperature levels in their processes. Kollmorgen also makes a valuable contribution to reducing heat input on the motor side due to the fact the highly efficient AKM servo motors keep thermal power losses low. The synchronous servo motors also operate without separate fans.
No brake power applied to hydraulics
The negative impact of heat on longevity and energy efficiency can also be felt beyond partial load and standby scenarios—namely when hydraulics themselves are subject to braking forces. Hainzl uses Kollmorgen technology for things like handling tasks within intralogistics processes, where heavy steel parts need to be raised and lowered. With a centralised hydraulics system, the kinetic energy generated during lowering can only be taken up via the oil in the form of heat. The consequences are those described—and may even include additional cooling measures, which only further reduce the overall efficiency of a machine (think OEE). "The electrohydraulic system developed jointly with Kollmorgen makes it possible to transfer braking energy directly to the motor," explained Schrenk. This gives the Austrians the option to feedback braking energy, particularly during constantly repeated lowering sequences, in a way that is elegant and (more importantly) energy efficient.
The bottom line
With the ready-made servo pump drive solution, Kollmorgen has developed a new functionality for electrohydrostatic actuators (EHAs) based on the S700 series of servo drives. The software-based application can be easily adapted to the specific features of the application at hand by setting the relevant parameters at the engineering stage. This means the benefits of EHAs can be exploited without having to consider the possible restrictions associated with existing centralised hydraulics arrangements. Kollmorgen is supporting this approach with a drive solution designed to be modular but, above all, open and which can be easily integrated into existing automation setups.
-
PPMA 2025
23 September, 2025, 9:30 - 25 September, 2025, 16:00
NEC, Birmingham UK -
Advanced Engineering Show 2025
29 October, 2025, 9:00 - 30 October, 2025, 16:00
NEC, Birmingham UK