- Home » Editorial » Hydraulics
How can optimisation of steel for piston rods improve the economics of hydraulic cylinders?
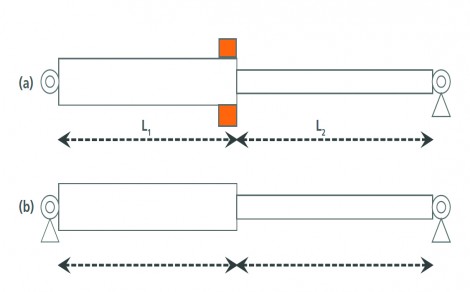
Mattias Awad, head of marketing and technology, OVAKO Cromax AB, explains how manufacturing piston rods from higher-strength steel can enable them to be downsized, reducing weight and costs while maintaining the required margin of safety against failure.
The forces in piston rods can be push (compression) or pull (tension). These forces are to a large degree axial and uniformly distributed over the rod section. In single-acting cylinders, the piston rod is usually loaded in push-only (compression) mode so fatigue is not an issue. In this case, the rod is dimensioned so that its axial stress remains below a level that will give rise to buckling. This is a sudden, large and unstable lateral deflection associated with only a small increase in compressive load above a critical level – the buckling load. The corresponding stress can be far less than the yield strength of the rod material. Once it occurs, buckling leads to instability and collapse of the piston rod. Hence, it is potentially a highly dangerous failure mode which can be the cause of serious accidents.
Piston rods in double-acting cylinders experience alternating compression-tension loads. So, in addition to a buckling risk on the compression part of the load cycle, the cylinder designer must also give consideration to the possibility for fatigue. Apart from the mechanical properties of the steel, other important factors related to the fatigue strength of piston rods are surface finish, stress concentrations and, for welded rods, weld quality.
Effective piston rod length
In terms of its tendency to buckle when loaded, the effective length of a piston rod depends on the cylinder mountings. If the cylinder is supported at the gland (Fig. 1 a) then the effective rod length can be approximated as the stroke. However, a very common arrangement is that the cylinder is mounted via pin and eye joints at the end of the rod and the bottom of the tube (Fig. 1 b). For this type of mounting, many designs are based on the standpoint that the effective length is (L1+L2). This is too conservative and results in an over-dimensioned piston rod.
Calculations for a range of dimensions and lengths for both piston rod and tube indicate that the effective piston-rod length for end mounting is about 1.6 times the actual length. This estimate furnishes a reasonably accurate and conservative evaluation of the buckling strength.
Optimised steel offers the possibility to downsize piston rods
Cromax 180X is a hard-chrome-plated bar based upon a medium-carbon micro-alloyed steel. Judicious control of minor alloy additions and optimised processing confer high strength to the base steel. The minimum yield strength of Cromax 180X is 500 MPa which can be compared with 305 MPa for grade C45E, a common steel selection for piston-rod applications. For Cromax 180X, this high level of yield strength is guaranteed in the finished, i.e. chrome-plated, condition.
Rods in Cromax 180X will exhibit better resistance to buckling than corresponding rods based upon C45E steel. Hence, for a given effective length, a rod of Cromax 180X can be reduced in diameter compared with one in C45E, while still maintaining the same margin of safety against buckling. This is demonstrated quantitatively in Fig. 2 which depicts the diameter decrease which is attainable when rods of C45E-steel are swapped for ones in Cromax 180X. The downsizing is given as function of rod length for three different diameters, 45, 63 and 90 mm.
Naturally, any reduction in rod diameter results in a corresponding reduction in weight of the rod. The percentage weight reduction corresponding to the downsizing depicted in Fig. 2 is shown as a function of effective length in Fig. 3.
In addition to the benefits of weight reduction, there are economic advantages due to reduced material costs. As an illustration of the potential – a piston rod in steel C45E, 63 mm diameter and effective length 1000 mm can be replaced by a rod in Cromax 180X with diameter 55 mm giving a weight reduction of 5.8 kg or 24 %.
As an alternative, if a rod in steel C45E is replaced by one made of Cromax 180X with the same diameter, then it can transmit a greater load while keeping the same margin of safety against buckling. Obviously, a redesign will be required to enjoy the benefit of the increased load rating, involving increased diameters of the tube, piston, gland and so on, which may not always be realistic or feasible.
Improved fatigue life
The fatigue failure of piston rods occurs either at locations where a reduced section is combined with stress-concentration, at threads for example, or at welds. Fusion-welded piston rods are particularly susceptible to fatigue failure because the welds contain crack-like defects, are characterised by unfavourable tensile residual stresses and very often do not penetrate the entire cross-section of the rod. It is for this reason that piston rods, which are subjected to high alternating loads and which carry an elevated risk for fatigue failure, are usually friction welded. A properly-executed friction-welded joint is virtually defect-free and extends over the entire cross-section of the rod; it is therefore characterised by far greater fatigue strength than a corresponding fusion weld.
Tests have shown that the higher tensile strength of Cromax 180X (min. 750 MPa) offers a better fatigue performance than rods made of the conventional grade C45E with minimum tensile strength 590 MPa. Hence, the desired fatigue resistance can be achieved using a smaller diameter rod with positive benefits for weight and cost.
Good and consistent machinability
The machinability of Cromax 180X has been documented by testing in turning and threading. This shows that the steel can be processed efficiently by machining, compared with hard-chrome bars based upon steel C45E even though its strength and hardness are considerably higher.
Fusion and friction welding
The weldability of steel used for piston rods is an important characteristic. In fusion welding, the primary metallurgical consideration is that the formation of hard, brittle constituents in the weld heat affected zone (HAZ) should as far as possible be avoided. Cromax 180X rods up to 60mm in diameter can be fusion welded without preheating; for larger diameters, preheating is recommended in order to counteract fast cooling after welding and so lessen the risk that brittle constituents are formed in the HAZ.
Welded piston rods subjected to heavy loads, especially reversed compression-tension loads, are best manufactured via friction welding. Correctly executed, such a weld has equivalent strength and fatigue resistance to the base steel in the rod. Cromax 180X is designed to mitigate the risk for HAZ-embrittlement in connection with friction welding.
Suitability for induction-hardening and cold-drawing
Cromax 180X in an induction-hardened execution is available for applications where there is risk for damage to the piston rod as a result of external impact. For piston-rod applications requiring extremely high strength, Cromax 180X can also be offered in a cold-drawn execution having a minimum yield strength of 690 Mpa which is on-a-par with quenched-and-tempered low-alloy steel with considerably higher alloy content, grade 42CrMo4 for example.
Summary – a new steel grade for piston rods
A new steel grade, 180X, is now available for piston-rod applications in hydraulic cylinders. In hard-chrome-plated execution, Cromax 180X is characterised by higher strength than traditional grades used for hydraulic-cylinder piston rods. The improved yield strength means that rods can be downsized without compromise to the margin of safety against buckling under axial compressive loads and against fatigue if the loads are alternating. This offers positive benefits for both weight and cost.
-
PPMA 2025
23 September, 2025, 9:30 - 25 September, 2025, 16:00
NEC, Birmingham UK -
Advanced Engineering Show 2025
29 October, 2025, 9:00 - 30 October, 2025, 16:00
NEC, Birmingham UK