- Home » Editorial » Hydraulics
New bearing technology helps boost pump and compressor output
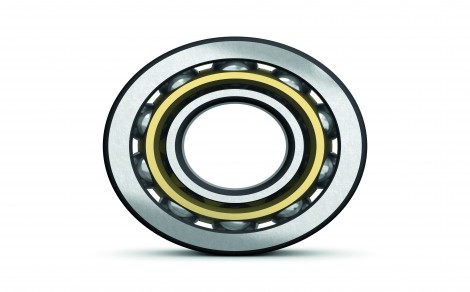
Pump and compressor manufacturers are now able to boost the output of their machines, both economically and without compromising reliability and efficiency, using a new design of single row angular contact ball bearings, writes Phil Burge, marketing and communications manager, SKF (pictured).
It is common practice in compressor and pump applications to raise the available power density of an installation by increasing its rotational speed. This does, however, pose challenges for pump and compressor shaft bearings, as increased speed inevitably results in raised bearing assembly temperatures.
Moreover, if the bearing’s cage design is unable to counter any dynamic instability within the assembly at higher speeds, the bearing arrangement will be subject to excessive vibration, precipitating mechanical damage and leading ultimately to bearing failure. Higher bearing speeds also raise the centrifugal forces acting on the rolling elements; this can alter the bearing’s design preload, generating friction and elevating the bearing’s operating temperature even further.
A new range of single row angular contact ball bearings has been developed with substantially increased limiting speed to address these issues, while also helping manufacturers to meet growing customer demands for higher levels of energy efficiency and in-service reliability. The new SKF Explorer class, single row angular contact ball bearings feature a 25° contact angle (the standard for this bearing type is 40°), a new cage design with stronger materials of construction and improved raceway geometry.
In high-speed applications the cage is a crucial bearing component, so for the new 25° contact angle, SKF has developed a stronger, low lead content brass cage with toroidal shaped cage pockets and an optimised cage pocket clearance. The 25° contact angle is an important development that SKF confidently believes will bring significant benefits to manufacturers of heavy-duty industrial pumps and compressor plant.
Application benefits
For multi-stage centrifugal pumps, for example, the new 25° contact angle standard offers an upgrade to the hydrodynamic/floating radial bearings that typically support the predominantly radial loads in these units. For double-suction impellers or closed impeller pumps, the 25° standard provides cooler running, substantially reduced vibration levels and extended service life in applications with high radial loads.
It is also possible to improve the robustness – and therefore the service life – of fluid handling applications or electric motors with vertical shafts and where the axial load is predominantly in one direction, with a bearing arrangement that includes a 40° contact angle unit taking the main load and a 25° unit acting as a back-up bearing.
Sealed variants of these new bearings are available for applications that may be more difficult to maintain, preventing contaminants from entering the bearing during installation and subsequent operation. Sealed SKF Explorer single row angular contact ball bearings have an attractive combination of design features such as low friction non-contact seals that ensure the same load carrying capacity as open variants.
At high speeds, the centrifugal forces within the bearing assembly can cause contact angle variations as the ball contact points between the inner and outer rings changes, causing the balls and rings to slide relative to one another. For applications with moderate axial loading, the new 25° contact angle reduces this effect, enabling the bearing to operate at higher speeds without risk of cage fracture.
The new raceway geometry also significantly minimises the risk of a phenomenon known as ‘ellipse truncation’ which can impose severe stress peaks during abnormal running conditions such as shock loading. Single row angular contact ball bearings with the new raceway geometry can accommodate axial forces as much as three times higher without ellipse truncation, compared to bearings with more conventional raceway designs.
Thanks to the optimised ball-to-cage contact geometry the temperature behaviour of this bearing at high speeds is more stable and the lubricant film formation is improved. Furthermore, noise and vibration levels are reduced by 15% and the limiting speed for the newly developed brass cage has increased by approximately 30% over that of previous designs.
-
PPMA 2025
23 September, 2025, 9:30 - 25 September, 2025, 16:00
NEC, Birmingham UK -
Advanced Engineering Show 2025
29 October, 2025, 9:00 - 30 October, 2025, 16:00
NEC, Birmingham UK