Return of the screw
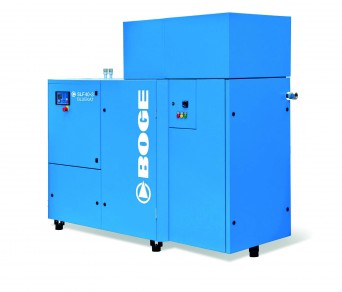
There are several fundamental air compression technologies available on the market. Carl Sharpe, UK & Ireland sales manager at Boge Compressors, outlines the case for the rotary screw.
Every compressor manufacturer will be delighted to extol the relative benefits of their own technology, while skating over its weaknesses. There’s nothing wrong with that: there are plenty of different ways to provide a supply of compressed air, and every system on the market is only there because it fulfils the needs of at least one group of end users. In many cases, there will be several different approaches that meet the requirements of the application.
One perennial debate in the industry is between vane and rotary screw designs. Both technologies operate with a continual rotary motion that reduces the volume of a space inside the compressor, squeezing the air inside to the desired pressure before releasing it into storage or distribution pipework. As their names suggest, one design achieves that change with two carefully shaped interlocking screws, while the other uses a shaft mounted eccentrically in a chamber, with sliding vanes that maintain contact between the hub and the chamber walls.
Rotary screw is the most popular and widely used technology on the market. There are good reasons for that. Rotary screw compressors are robust, flexible and efficient. They are suitable for an extremely wide range of applications and available in sizes and configurations to suit the requirements of the vast majority of users. The rotary screw design is quiet and smooth running, which makes installation straightforward, even in noise- or vibration- sensitive environments.
High pressures
Indeed, the rotary screw has characteristics that make it the only choice for some applications. The first of those is where high pressures are required. Vane technologies work best at pressures of up to 10bar, while rotary screws operate routinely at up to 13bar and some models can be configured to deliver 15bar or more.
Then there is oil-free air. Vane designs require oil lubrication to facilitate vane motion and maintain a low-friction seal between the vanes and compression chamber wall. Rotary screws, by contrast, are available in oil-lubricated or oil-free designs. For some end users – such as those in the electronics, food production or pharmaceutical sectors, oil-free air is widely required. It is becoming increasingly popular in other sectors too, as companies seek to drive up product quality and reduce environmental contamination.
But assuming your application has lower maximum pressure requirements and can accommodate oil lubrication, either technology would be applicable. If that’s the case, then factors such as reliability, energy efficiency and total cost of ownership become decisive. And those things are determined not by the fundamental compression technology, but by the overall design, operation and maintenance of the complete compressed air system.
Longevity
Take longevity, for example. One potential benefit of the vane design is that the shaft experiences small radial loads. Compressors of this design can support their shafts with simple plain bearings that usually last the lifetime of the machine. That doesn’t mean vane compressors are maintenance free, however. Compressors are long-lived, hardworking machines and all designs require parts such as seals to be replaced periodically. What matters more is how easy that work is to do, how often it is required, and how much it costs. And that is down to the details of individual compressor design and manufacture, regardless of type.
Efficiency
Then there’s efficiency. Manufacturer efficiency claims are often based on the operation of machines at a single carefully selected speed. Every model has an operational sweet spot where it works at its best. The end user needs to understand the efficiency that will be delivered by the system in their application under real-world operating conditions. That’s going to depend on a host of factors, including whether a particular manufacturer has a model that provides a close match, and how the whole compressed air installation is designed and operated.
In summary, in the choice between vane and screw compressors, your application might determine the answer for you. If you need high pressures or oil free air, you need a screw design. Where either technology could do the job, it’s time to worry less about the fundamentals and more about the details of the particular machine, the overall compressed air installation and, of course, the support and experience of your supplier.
-
PPMA 2025
23 September, 2025, 9:30 - 25 September, 2025, 16:00
NEC, Birmingham UK -
Advanced Engineering Show 2025
29 October, 2025, 9:00 - 30 October, 2025, 16:00
NEC, Birmingham UK