Lifting the lid on vane compressor efficiency
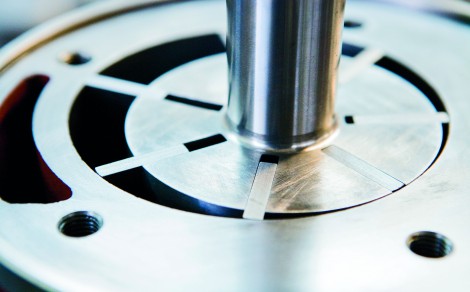
In today’s market, there is a choice of two main types of industrial rotary compressor – vane and screw. Although both are designed to produce the same output (compressed air), they can differ considerably in terms of energy efficiency. Andy Jones, managing director at Mattei, shows how the design of vane air compressors can make a big difference.
The choice confronting plant managers when selecting an industrial rotary compressor is between two different types of compressor technology. Designed to produce the same end result, vane and screw technologies actually differ quite considerably.
Over the years, screw compressors have proven more popular. However, their widespread use has more to do with the screw being cheaper and easier to replicate than technological advantage.
With energy efficiency now a critical consideration being pushed at both a regulatory and business level, it’s time to re-examine the fundamental benefits of vane compressor design in terms of efficiency, longevity and maintenance.
Different options
A rotary-vane compressor comprises a rotor, with slots along its sides which house individual sliding vanes. This assembly is offset within a cylinder, or ‘stator’, and rotates on white-metal bushes. As the rotor turns on its axis, the vanes are pushed against the stator wall by centrifugal force and the air is compressed.
In comparison, a screw compressor has two parallel rotors – a male and a female – which engage into each other. These two rotors intersect longitudinally with a critical minimal clearance, and in turn are fitted into a stator. During rotation, the profiles mesh into each other, compressing the air.
So, what does this mean for efficiency? Let’s look at the key ways in which vane compressors can reduce power consumption, improve durability and provide long-lasting performance.
Efficient design
Vane compressors have an inherent advantage over screws because their design eliminates ‘blowholes’ where air under high pressure can be driven to areas of low pressure, which is inherent in screw compressors.
This means that vane compressors don’t need to run at high speeds to compensate for air leakage. They can operate at low speeds, from a direct drive coupling, which in turn leads to lower power consumption.
Furthermore, oil is injected into the stator to seal clearances between the rotor, stator and end covers. The oil serves to lubricate the moving parts and cool the air during compression, keeping the freely moving vanes in constant contact with the stator’s internal surface, so the air seal is near perfect.
Improved resilience
Another important benefit of the lubricating oil is that it forms a film on which the vanes slide. With no direct metal-to-metal contact between the vanes and the internal stator wall there’s no negative wear.
In fact, rather than experiencing damaging wear, the blades of a rotary vane compressor undergo a polishing process during use, which results in less friction, and consequently, better operation and reduced energy requirement.
The impact of this process on the durability of the product is startling. Some vane compressors have been known to run for over 200,000 hours without the need to replace the white-metal bushes used in this type of compressor.
In contrast, bearings, which play a critical role in screw compressor performance, are typically required to be replaced at every 30,000-40,000 hours. Bearing-related problems can significantly impair compressor reliability and in the worst case they can lead to catastrophic failure.
Long-lasting performance
The polishing effect discussed above means that efficiency actually improves for the first thousand hours or so and then stays constant throughout the rest of its operating life, whereas typically a screw compressor's efficiency falls away over time as its bearings wear. This fact alone can mean a significant saving on compressor ‘Life Cycle Costs’ when choosing a vane compressor instead of a screw compressor.
If a rotary vane compressor is looked after in accordance with manufacturer’s instructions the operating life of its airend can easily extend to over 100,000 hours without wear, even in dusty operating conditions.
Energy efficiency is a serious priority for the industry, and air compressors play a major role in reducing consumption. With its energy efficient design, vane air compression technology can help businesses minimise their energy use whilst lowering the cost of ownership throughout a unit’s lifespan.
-
PPMA 2025
23 September, 2025, 9:30 - 25 September, 2025, 16:00
NEC, Birmingham UK -
Advanced Engineering Show 2025
29 October, 2025, 9:00 - 30 October, 2025, 16:00
NEC, Birmingham UK