Lifting the lid on vane compressor efficiency
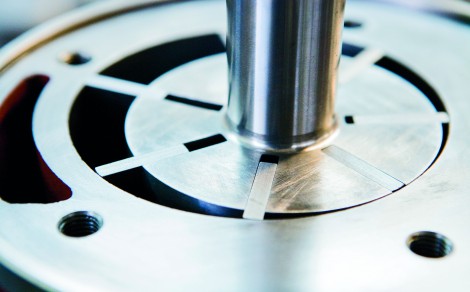
The impact of this process on the durability of the product is startling. Some vane compressors have been known to run for over 200,000 hours without the need to replace the white-metal bushes used in this type of compressor.
In contrast, bearings, which play a critical role in screw compressor performance, are typically required to be replaced at every 30,000-40,000 hours. Bearing-related problems can significantly impair compressor reliability and in the worst case they can lead to catastrophic failure.
Long-lasting performance
The polishing effect discussed above means that efficiency actually improves for the first thousand hours or so and then stays constant throughout the rest of its operating life, whereas typically a screw compressor's efficiency falls away over time as its bearings wear. This fact alone can mean a significant saving on compressor ‘Life Cycle Costs’ when choosing a vane compressor instead of a screw compressor.
If a rotary vane compressor is looked after in accordance with manufacturer’s instructions the operating life of its airend can easily extend to over 100,000 hours without wear, even in dusty operating conditions.
Energy efficiency is a serious priority for the industry, and air compressors play a major role in reducing consumption. With its energy efficient design, vane air compression technology can help businesses minimise their energy use whilst lowering the cost of ownership throughout a unit’s lifespan.
-
PPMA 2025
23 September, 2025, 9:30 - 25 September, 2025, 16:00
NEC, Birmingham UK -
Advanced Engineering Show 2025
29 October, 2025, 9:00 - 30 October, 2025, 16:00
NEC, Birmingham UK