For highest performance and precision, use closed-loop control
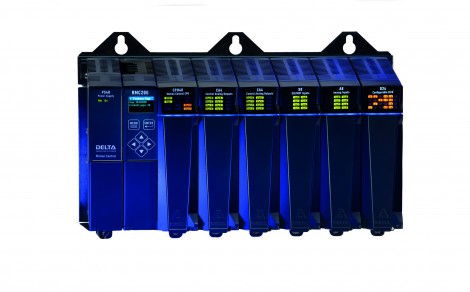
By Tim Gessner, Ph.D., Delta Computer Systems Inc.
Hydraulics has always been great for pressing, lifting or holding heavy loads, but fluid power has not traditionally been thought of as a power source for precise motion. In the past, many hydraulically-driven machines used two-position actuators with motion limit switches.
The sound and shock of these actuators inspired the nickname ‘bang-bang’ control for these systems. But with advances in motion control technologies, fluid power control systems have come a long way. These technologies open up new opportunities for improving productivity and cutting life cycle costs for machine builders. The key to advanced motion control is choosing the right components and effectively programming the motion controller.
The newest electrohydraulic motion controllers can be configured to employ sophisticated predictive algorithms, using inputs from both position and pressure sensors to provide tighter control and smoother operation than was previously possible with hydraulic control systems. And with millisecond control loop times, these controllers produce more precise motion under a wider range of conditions than is achievable with PLCs.
Closed-loop versus open-loop control
A caveat, however – fluid power applications provide some of the most complex motion control problems, because the medium involved (air or hydraulic oil) doesn’t respond to control inputs in a perfectly linear manner. Using feedback in closed-loop control can provide the smoothest, most precise motion, but this requires a motion controller that is able to take best advantage of the feedback information.
Open-loop systems, those not incorporating feedback, may not require the setup and programming of a closed-loop motion system, but they also don’t have the advantage of the flexibility and precision that using closed-loop control provides. Applications requiring profile-following, synchronisation or gearing the motion of one axis to that of another must use closed-loop control. The same applies to those requiring a high degree of operational flexibility or speed with accuracy, and those applications needing the ability to maintain precision with changing loads or environmental conditions. Table 1 summarises the advantages and challenges of closed-loop motion control.
Choosing system components and setting up a closed-loop system
Figure 1 contains the block diagram of a typical electrohydraulic control system. Cylinder position information is provided to the motion controller by a linear magnetostrictive displacement transducer (LMDT) that is mounted in the cylinder. LMDTs are used in precision hydraulic control systems because they don’t require a homing step and they report the absolute position of the cylinder. For force feedback, two pressure transducers are mounted in each cylinder, one on each side of the piston. The difference in pressure readings is the force being applied by the cylinder. Hydraulic fluid flow is governed by a proportional servo valve, which is capable of making minute adjustments to flow under control by the motion controller. Designers should select servo-quality valves with zero spool overlap and a linear response so that they respond well to control inputs (i.e., with no gain changes or ‘dead bands’ in the control range).
Cylinders, valves, pumps and accumulators used in closed-loop systems must be sized large enough to allow for quick acceleration and positioning of the actuator. Hose runs should be short, and metal tubing should be used where possible, with as few bends as possible, in order to reduce the amount of fluid compression and expansion which can affect controllability.
Programming and tuning the motion
Key to setting up the motion is the application development tool set. In the case of Delta Computer Systems’ motion controllers (an example is the RMC200 shown in Figure 2), that tool set is the RMCTools package, provided free with the company’s controller products. Rather than requiring the use of low-level machine code as is the case with many other motion controllers, this development environment includes graphical tools for programming, troubleshooting, and tuning motion algorithms. RMCTools allows motion sequences to be set up by filling out forms and selecting intuitive options from pull-down menus (See Figure 3).
Once the motion steps are programmed, the system must be tuned for optimal operation. For this step of the development process, the RMCTools package provides software for analysing the motion and adjusting control loop gains. The software contains a Plot Manager for displaying motion parameters versus time, and a Tuning Wizard (Figure 4) to simplify the tuning process.
Hydraulics advantages summarised
Hydraulic motion control offers many benefits over electric motor control, especially when working with high-speed linear travel, heavy loads or when very smooth position or pressure/force control is required. By selecting appropriate system components and programming your motion controller to use the correct closed-loop motion control algorithms, the result can be a system that offers high performance and very precise motion at a reasonable cost.
-
Farnborough International Airshow
22 - 26 July, 2024
Farnborough International Exhibition & Conference Centre