- Home » Editorial » Hydraulics
Three common methods of establishing fuel or oil cleanliness levels
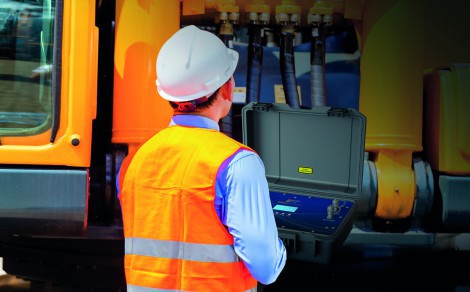
By Richard Price, managing director, Filtertechnik.
At a time when most industrial, agricultural and construction equipment is more sophisticated than ever, the demands on maintenance staff are higher than ever. Modern equipment is less tolerant to dirty and contaminated fuel, lubricating oil and hydraulic oil than previous generations of equipment. 85% of lubrication related equipment failures are caused by water or particulate contamination.
It therefore follows that the key to effective preventative maintenance hinges on a sensible and practical process of establishing oil and fuel cleanliness levels. There are three common methods of establishing fuel or oil cleanliness levels, each with their own advantages. These are:
1. Oil sampling and analysis for particulates and water.
2. Real-time FS9V2 Particle Pal counter for particulate, water & density.
3. Patch test kit for type and size of contaminant.
Oil sampling and analysis
Many mobile equipment manufacturers and third-party providers sell oil sampling kits that include the analysis and a detailed report. Proper oil sampling is critical to an effective oil analysis programme. Using a sample pump is an easy way to get a representative sample form either a tank or through a test point in a hydraulic line in any piece of mobile industrial, agricultural or construction equipment. The sample is posted to a central lab, using sample bottles and packaging supplied in the kit, which uses a sophisticated spectrometer to analyse the fuel or oil sample. Spectrometry allows the lab to identify and quantify wear metals, oil additives, solid contaminants, dirt and water in the sample making oil analysis a useful service in predicting potential problems in machines of all types. To maximise the benefit of oil sampling a process of taking regular samples and building up a medium-term picture of trends is recommended.
Real-time FS9V2 Particle Pal counter
This versatile self-contained instrument can be used for oil and fuel on-site, in process engineering, by a manufacturer for R & D or quality control purposes or in a laboratory. The big advantage of the Particle Pal is its ability to give an instant cleanliness reading allowing an operator to have a clear and accurate picture of the cleanliness levels of his oils or fuels.
The instrument can display ISO, NAS and SAE cleanliness readings and the option of water content analysis for oils and/or diesel fuels. Complete with a re-chargeable battery, high pressure internal gear pump and controlled flow rate. Whether on-site or in the laboratory, the Particle Pal will provide cleanliness readings in real time to allow an engineer to fully understand the condition of their oils or fuels.
The FS9V2 units now have a single LCD display showing all the connected sensors in real time. Filtertechnik has added an internal memory for capturing data with a simple USB data transfer of results that can be printed showing tabular and graphical results. Also included is powerful trending software which shows real time cleanliness data in graphical format via USB transfer to a connected PC.
Patch test kit
A patch test kit provides everything that’s needed to make an enterprise self-sufficient in identifying the type and level of contamination in fluid power systems in a process or manufacturing environment. Patch testing allows rapid testing and analysis and it is very effective in determining the source of contamination, in a manufacturing process for example.
The testing process starts with a representative oil sample being taken from a reservoir or from a Minimess test point in a hydraulic circuit. A sample of the fluid is passed through a filter membrane, using a vacuum pump, dried and mounted in a membrane holder ready for a visual assessment under a digital microscope. Comparator slides are used to help establish cleanliness levels in the sample. The supplied filter colour rating and particle assessment scales correspond to ISO 4407, the international standard for particulate contamination of fluids determined by the counting method using a microscope.
-
PPMA 2025
23 September, 2025, 9:30 - 25 September, 2025, 16:00
NEC, Birmingham UK -
Advanced Engineering Show 2025
29 October, 2025, 9:00 - 30 October, 2025, 16:00
NEC, Birmingham UK